Tres finales para una misma historia: ventajas del modelo de mantenimiento preventivo frente al correctivo.
Mantenimiento correctivo
Jueves por la noche, el tercer turno de la jornada acaba de iniciar sus actividades del día en la planta. El encargado de producción se sienta frente a las pantallas del sistema SCADA para verificar que todos los procesos se encuentren dentro de los parámetros habituales. Mientras revisa el reporte del turno anterior, una alarma empieza a parpadear en uno de los CCM del sector de empaque de productos.
El encargado toma la radio para comunicarse con el responsable de mantenimiento eléctrico que se encuentra en campo realizando una revisión rutinaria. La respuesta es breve: la línea está parada porque dejó de funcionar uno de los arrancadores suaves instalados en una de las numerosas ampliaciones realizadas hace un par de años en el sector de la planta que maneja el agregado de ingredientes secos (polvos) a la preparación.
El responsable de automatización
inicia el software de ingeniería de su estación de trabajo mientras ve cómo las alarmas del sector de empaque se van encendiendo una tras otra. Una vez que tiene acceso al software de ingeniería y se conecta a la red, encuentra el buffer de diagnósticos del PLC lleno con infinidad de mensajes crípticos, y no tiene tiempo de descifrarlos; la otra línea de empaque está trabajando al límite, por lo que es vital centrar su atención en la línea parada. Verifica cuál es el tag del nodo de la red Profibus DP que conecta todos los arrancadores, drives y monitores de energía de la red que conecta al CCM con el sistema de control. Luego abre el plano de la red en AutoCad para localizar dónde se encuentra el dispositivo con problemas. Mientras se pregunta la causa detrás de las múltiples alarmas también trata de recordar si se efectuó algún cambio reciente en las redes de proceso del sector.
En ese momento se da cuenta de que el plano está desactualizado, uno de los segmentos de red correspondiente a la última ampliación aún no fue incorporado al plano general.
El responsable de mantenimiento eléctrico recibe la orden de localizar el equipo problemático, pero toda la documentación con la que cuenta es un esquema apresurado realizado en una hoja de papel que le dejó la empresa de montajes eléctricos que realizó una visita a la planta tres semanas atrás.
En este esquema, los dispositivos están identificados por su dirección Profibus DP, pero el esquema no contiene detalles acerca del tipo de nodo que corresponde a cada dirección. Mientras empieza a abrir un gabinete tras otro tratando de encontrar el nodo defectuoso, se dispara una alarma en el transportador que lleva el producto desde la salida del sector de producción hasta el sector de empaque.
Para evitar el desborde de producto en el transportador, equipado con balanzas de pesaje continuo, tras realizar una medición fuera de escala, activó el sistema de seguridad de la planta: la planta se encuentra en una parada de emergencia. La producción se ha detenido. Decide llamar al jefe de mantenimiento para ponerlo al tanto del problema en el que se encuentra.
Mientras tanto, el personal de mantenimiento eléctrico de la planta pasa toda la noche desmontando el motor controlado por el arrancador y descubren que había estado trabajando sobrecalentado durante los últimos días, hasta que la alta temperatura dañó la placa electrónica de control. El motor está dañado y es irreparable. El pañol de repuestos acaba de pedir un reemplazo de urgencia, pero el proveedor certificado no responderá hasta la mañana siguiente.
El jefe de mantenimiento tiene la desagradable tarea de informar a la gerencia que la planta se encuentra parada y que el arranque requiere de varias tareas de mantenimiento que llevarán, por lo menos, 24 horas. Su mente empieza a hacer cálculos sobre las horas de producción perdidas y su equivalente en términos de ingresos perdidos.
Mantenimiento correctivo con diagnóstico
Jueves por la noche, el tercer turno de la jornada acaba de iniciar sus actividades del día en la planta. El supervisor de instrumentos se sienta frente a las pantallas del sistema SCADA para verificar que todos los procesos se encuentren dentro de los parámetros habituales. Mientras espera que el agua para el mate se caliente, una alarma empieza a parpadear en uno de los CCM del sector de empaque de productos.
El supervisor toma la radio para comunicarse con el responsable de mantenimiento eléctrico que se encuentra en campo realizando una revisión rutinaria. La respuesta es breve: uno de los arrancadores suaves instalados la semana pasada en la reciente ampliación del sector dejó de funcionar y la línea está parada.
El supervisor inicia el software de ingeniería de su estación de trabajo mientras ve cómo las alarmas del sector de empaque se van encendiendo una tras otra. Una vez que tiene acceso al software de ingeniería y se conecta a la red, encuentra el buffer de diagnósticos del PLC lleno con infinidad de mensajes crípticos, y no tiene tiempo para descifrarlos; la otra línea de empaque está trabajando al límite, por lo que es vital centrar su atención en la línea parada. Verifica cuál es el tag del nodo de la red Profibus DP que conecta todos los arrancadores, drives y monitores de energía de la red que conecta al CCM con el sistema de control, y luego abre el plano de la red en AutoCad para localizar dónde se encuentra el dispositivo con problemas.
El supervisor recuerda que hace unos días llegó a la planta el equipo de diagnóstico de redes Profibus DP que había solicitado al sector Compras hace medio año. Intenta recordar las instrucciones que recibió durante el curso de entrenamiento que hizo hace más de tres meses mientras se dirige al sector y pasa por el pañol de instrumentos para retirar dicho equipo.
Llega al sector y decide conectarse a la red Profibus DP mediante el único conector DB9 apto para diagnósticos, el cual la empresa de montaje olvidó retirar. Después de conectar la laptop de servicio al equipo, realiza un chequeo rápido del segmento y descubre que es el nodo 7 el que presenta mensajes de error y diagnóstico. Procede a ver qué tag corresponde a dicho nodo e informa por radio a producción que disminuyan la carga del transportador para no saturar el sector de empaque.
El mensaje llega a tiempo y la planta se mantiene activa, aunque con un nivel de producción reducido.
El personal de mantenimiento ubica el gabinete correspondiente al dispositivo con problemas y descubre que presenta daños por sobrecalentamiento. Hay que reemplazar la placa electrónica de comunicaciones, pero el motor sobrevivió aunque haya trabajado casi al límite. El responsable de mantenimiento eléctrico consulta el stock del pañol de repuestos y confirma que cuenta con una placa de comunicaciones de repuesto, pero debe esperar al turno siguiente para que el programador verifique el sistema y pueda ayudar a definir cómo se produjo el inconveniente.
La planta vuelve a arrancar después del mediodía del viernes, acumulando doce horas de producción perdida.
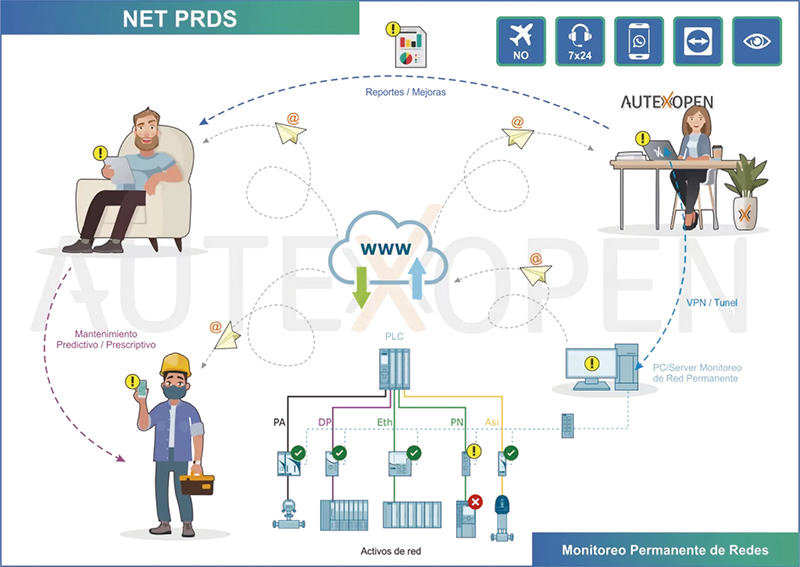
Mantenimiento en la era de la pandemia y la pospandemia
Muchas tareas de mantenimiento que hasta hace un par de meses eran rutinarias, ahora requieren de un planeamiento cuidadoso y una ejecución sin margen para errores
Martes por la tarde, se acerca el final de jornada para el segundo turno de trabajo en la planta. Muchas tareas de mantenimiento que hasta hace un par de meses eran rutinarias, ahora requieren de un planeamiento cuidadoso y una ejecución sin margen para errores.
La planta se encuentra trabajando a niveles de productividad casi iguales a los del año pasado a esta altura, pero con una tercera parte del personal ausente. Debido a los requerimientos de distanciamiento social, tanto en la planta como en las oficinas administrativas, y dada la complejidad de la logística necesaria para realizar el traslado de personal desde y hasta la planta, todas las tareas compatibles con la modalidad de acceso remoto se han adaptado a esa modalidad.
Bajo estas condiciones, eventos tales como fallas imprevisibles o paradas de emergencia implican costos inadmisibles. El acceso a repuestos y reemplazos de material se ha complicado de manera creciente en los últimos días, lo que implica que los conceptos que definen el mantenimiento predictivo dejaron de ser algo abstracto y se transformaron en una necesidad real de cada día.
Los conceptos que definen el mantenimiento predictivo dejaron de ser algo abstracto y se transformaron en una necesidad real de cada día
El supervisor de instrumentos revisa por última vez en el día el estado del sistema de control, y verifica el plan de trabajo programado para el personal de mantenimiento. La coordinación entre los distintos grupos de trabajo y los turnos ha mejorado drásticamente en las últimas semanas. Muchas modalidades de trabajo consideradas incompatibles con el entorno industrial ahora se implementan por necesidad. El acceso remoto a los recursos se considera siempre como la primera opción.
Las tradicionales objeciones al acceso remoto, tales como la consiguiente disminución de la seguridad de los sistemas de TI corporativos, se van resolviendo sobre la marcha mediante un cuidadoso y metódico monitoreo de los parámetros de su funcionamiento.
El último reducto al modo de trabajo remoto, las redes de los sistemas OT de planta, también se están adaptando a este nuevo estado de las cosas. Por supuesto que las tareas operativas de control se realizan localmente, pero muchas tareas de monitoreo preventivo se realizan de manera remota y, en algunos casos, de manera tercerizada.
Muchas tareas de monitoreo preventivo se realizan de manera remota y, en algunos casos, de manera tercerizada
Cuando el supervisor está por retirarse, recibe un mensaje en su teléfono celular. Es una alerta emitida por el servidor web integrado en el monitor de la red Profibus DP instalado en el gabinete de control del sector de empaque. Es un e-mail generado automáticamente cada vez que el dispositivo detecta un cambio en el funcionamiento de la red. El supervisor abre en su estación de trabajo el navegador, y carga la página del monitor de red. Tras revisar los datos disponibles descubre que desde hace un par de horas uno de los nodos de la red ha estado generando alarmas correspondientes a diagnósticos internos.
Aunque estas alarmas tienen inicialmente un propósito informativo, el monitor de red activa la función de captura de telegramas en cada evento. Cuenta con un buffer que almacena los telegramas de intercambio de datos por períodos de tiempo antes y después de cada evento detectado, a fin de que se pueda realizar un análisis de cada evento mediante el análisis de la secuencia.
Después de los problemas que surgieron durante los primeros días de la pandemia, tanto el personal de mantenimiento como el de instrumentación y control, asistieron a entrenamientos remotos sobre las tecnologías empleadas en la planta. Estos entrenamientos siempre habían sido postergados por distintos motivos, pero la disponibilidad de tiempo adicional durante el primer par de meses permitió implementar estos cursos de manera remota.
En base a lo aprendido en estos entrenamientos, el supervisor da un vistazo a la captura de datos correspondiente a uno de los eventos, que se muestra en la aplicación de diagnóstico instalada en su estación de trabajo. Descubre que el nodo #9, correspondiente al arrancador suave con el tag “609e” emite una alerta de diagnóstico interno extendido de manera aleatoria desde hace algunas horas.
Casi simultáneamente recibe un mensaje del proveedor de servicios de monitoreo remoto contratado recientemente, informándole que sería recomendable verificar el estado de mantenimiento y el rendimiento del nodo #9 del sector de empaque, poniendo atención especial en la temperatura del nodo y su entorno, ya que la captura de datos asociada a los eventos de alarma indica que dicha alarma corresponde a un diagnóstico interno asociado al sensor de temperatura del motor.
El supervisor se comunica por radio con el responsable de mantenimiento, quien se dirige al gabinete correspondiente y descubre una gruesa capa de polvo sobre la cubierta del motor manejado por el nodo #9. El filtro de aire del sistema de ventilación del CCM estaba montado incorrectamente y permitía la entrada del polvo presente en el sector al gabinete, después de lo cual se depositaba sobre todas las superficies expuestas.
El sector de mantenimiento se encarga de reemplazar el filtro y limpiar el área. Una vez realizada esta tarea, no se registran más alarmas de diagnóstico relacionadas con el nodo #9.
El supervisor de instrumentos se retira de la planta una hora y media después del final de su turno, mientras coordina con su par del tercer turno las tareas de mantenimiento necesarias, poniendo punto final al incidente. El servicio de diagnóstico externo envía un mensaje indicando que el estado de la red ha regresado al estado normal y que no se presentan más alarmas. Las tareas de mantenimiento no requirieron la interrupción de los procesos productivos de la planta, que siguió operando a plena capacidad todo el tiempo.
Por Autex