Con un grado de automatización del 95 por ciento, la planta de fabricación de carrocerías de Scania en Oskarshamn, Suecia, es una de las plantas de automoción más modernas del mundo. Con máxima individualización: al final de la línea de montaje, ninguna cabina de camión es igual a otra. ¿Es esto ya la Industria 4.0? Los productos de automatización de Festo conforman una sólida base para ello.
Scania lleva ensamblando desde 2016 cabinas de camiones personalizadas tras recibir los pedidos, prácticamente sin excepción con la ayuda de 288 robots. “Para mí está muy claro que un producto de alta calidad debe producirse en una fábrica de alta calidad”, explica Marcus Holm, director de la fábrica de producción de cabinas de Scania en Oskarshamn. El alto grado de automatización conduce a una alta calidad, a buenas condiciones laborales y a la ergonomía para los trabajadores, agrega.

La fábrica del futuro
Los robots equipan las unidades de fijación con las piezas de chapa para mecanizar y las sueldan. Los trabajadores solo se encargan de cargar las estaciones y de vigilar las máquinas. La seguridad laboral sueca ha prohibido el uso de equipos de soldadura manual. Por un lado, los equipos de soldadura son demasiado pesados y difíciles de manejar, y por otro lado, las directivas de seguridad laboral exigen una distancia mínima entre la pinza de soldadura y el operador debido a la radiación.
Scania se beneficia doblemente de la prohibición de ejecutar trabajos de soldadura manuales en las líneas de montaje: “Esto mejora los procesos y la calidad”, recalca Lars Kreutner, director de proyectos para la fabricación de carrocerías para cabinas de Scania en Oskarshamn. Para aprovechar al máximo la técnica de automatización, Scania creó un área de formación en la que los empleados aprenden a usar los robots y la técnica de automatización.
Numerosas variantes posibles
Scania solo construye camiones con un peso total superior a 16 toneladas. La empresa se ha forjado una buena reputación como fabricante de vehículos especiales, por ejemplo, para cuerpos de bomberos o la recogida de residuos. Tan solo estos nichos de mercado crean cientos de miles de variantes.
“Puede resultar sorprendente, pero ofrecemos más opciones de personalización de camiones que las que existen en la fabricación de automóviles”, explica Evert Forsberg, ingeniero eléctrico y de automatización para prensas y carrocerías de Scania. En la producción de automóviles, cada modelo tiene su propia línea de montaje. “Por el contrario, nosotros ensamblamos todas las cabinas de conductor ofrecidas por Scania en una única línea de ensamblaje”, afirma Forsberg.
Industria 4.0 en acción
De este modo, la fábrica presenta características esenciales de la Industria 4.0: producción en masa de vehículos personalizados, capacidad de adaptación y flexibilidad gracias a la tecnología de control, capacidad de diagnosis, eficiencia energética y soluciones de seguridad. “Todos los fabricantes de equipos se rigen por un concepto de estandarización modular”, explica Forsberg. Al fin y al cabo, los operarios de los equipos deben poder confiar en productos de automatización de eficacia probada. El objetivo consiste también en no acumular innecesariamente un exceso de piezas de repuesto. Todas las piezas de chapa se sujetan en dispositivos controlados neumáticamente, donde se sueldan. “Nos decantamos conscientemente por los terminales de válvulas preconfigurados de Festo del tipo CPX/VTSA”, dice el experto en automatización Forsberg: “Nos ofrecen varias ventajas, desde la conexión Ethernet y la interfaz web hasta la diagnosis, la seguridad y Profinet o la eficiencia energética”.
De hecho, el terminal de válvulas CPX/VTSA es la única interfaz a Profinet, lo que elimina la necesidad de un cableado adicional. A través de la plataforma de automatización CPX, el terminal de válvulas ofrece datos de diagnosis con los que se pueden evaluar los equipos a modo de mantenimiento predictivo: “Podemos sustituir componentes de los equipos antes de que fallen y paralicen partes completas del equipo”, explica el director de proyectos Kreutner.
Diferentes zonas de presión
“También nos convenció el concepto de seguridad del terminal de válvulas”, comenta Forsberg. El CPX permite operar diferentes zonas de presión y purgar áreas cuando es necesaria una intervención. “De esta forma, podemos verificar las partes afectadas del equipo con paneles móviles y no tenemos que buscar fallos en todo el sistema a ciegas”. La nueva presurización de partes individuales del equipo resulta mucho más eficiente, desde el punto de vista energético, que arrancar el sistema completo.
Los robots de soldadura necesitan aire comprimido para ejecutar los movimientos de las pinzas de soldadura y para sujetar las chapas. El agua refrigerante protege los equipos de soldadura contra el sobrecalentamiento. Las soluciones completas para la alimentación de aire comprimido y de agua refrigerante para las pinzas de soldadura proceden de Festo. En Scania están integradas en la valla de seguridad de una manera fácil de usar, incluida la preparación del aire comprimido de la serie MS.
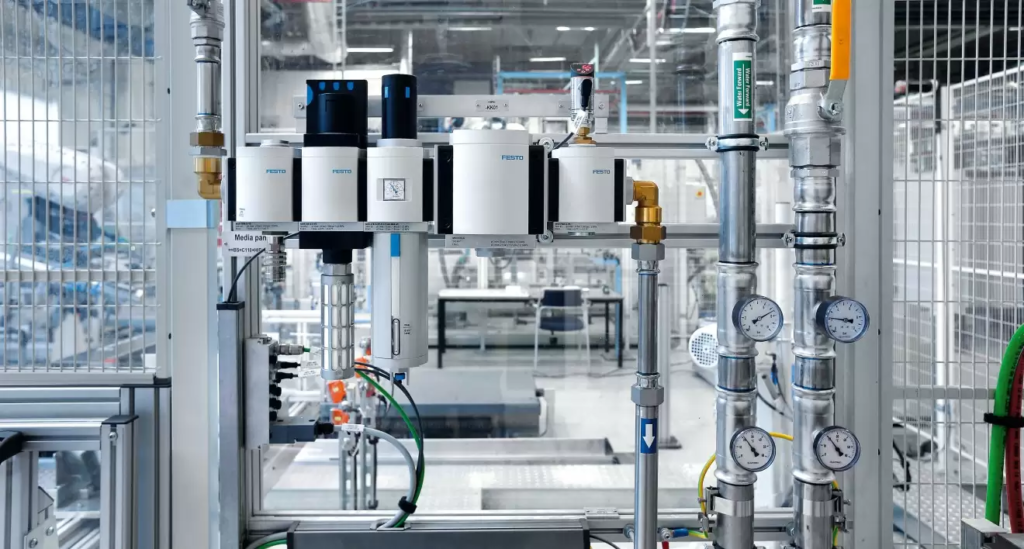
Fresado de electrodos seguro
Para las instalaciones de pinzas de soldadura fijas Festo desarrolló un brazo giratorio, según las especificaciones de Volvo y ABB, que acerca la fresadora de electrodos Tip Dresser a los electrodos después de cada 150 puntos de soldadura aplicados. El brazo giratorio funciona con cilindros eléctricos DNCE de posicionamiento preciso accionados por el motor paso a paso EMMS. Con esta solución, Festo reduce los tiempos de ciclo más de la mitad.
Trasfondo: con el paso del tiempo, los electrodos de una pinza de soldadura se desafilan y deben fresarse después de aproximadamente 150 puntos de soldadura para recuperar su precisión. “Fresar un electrodo es como sacarle punta a un lápiz”, explica Leif Lindahl, antiguo Key Account Manager para Scania en Festo.
El armario de maniobra de Festo para el fresado de electrodos comprende los controladores de motor CMMS y el CPX, que se comunica con los controladores de motor y el controlador de robot de nivel superior a través de Profinet. “Tampoco descuidamos el tema de la seguridad: los operarios ya no tienen que entrar en las células de los robots después del fresado para ajustar los electrodos a la posición correcta del punto de soldadura”, añade Lindahl.