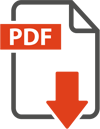
En este artículo, una presentación del trabajo final de Pablo Morales, ingeniero de YPF Upstream, en el marco del posgrado de Especialización en Automatización Industrial de la Facultad de Ingeniería de la Universidad de Buenos Aires.
En los comienzos de explotación de un yacimiento de petróleo o gas, la energía propia del reservorio permite la fluencia de los fluidos desde el fondo del pozo hasta la superficie en forma natural. A medida que el yacimiento se desarrolla, esta energía comienza a disminuir al igual que su producción. En estos casos se recurre a la sistemas de extracción artificiales tales como bombeo mecánico, bombeo electrosumergible, plunger lift, compresores de boca de pozo, entre otros. Para poder definir el sistema de extracción que se instalará en un pozo es necesario, entre otras variables, conocer su productividad.
Ya en superficie e independientemente del tipo de extracción, el fluido se transporta a las unidades primarias de tratamiento: el petróleo a las baterías, y el gas, a las unidades de separación primaria (USP). En ellas se realizan separaciones del tipo líquido-gas y líquido-líquido, se miden las fases, se contabiliza la producción total y finalmente se envía el producto de interés a las plantas de tratamiento de crudo (PTC) o de gas (PTG). Si el gas tiene menos presión de la requerida para ingresar a la PTG, primero se envía a una estación compresora (EC).
La laminación de un gas es una situación no deseable […] ya que se pierde parte de la energía entregada por los compresores que lograron llevar el gas a un estado de mayor presión.
La estación compresora cuenta con máquinas de desplazamiento positivo o compresores alternativos reciprocantes en los que, por medio de un pistón, se eleva la presión de sucesivos volúmenes de gas hasta un valor determinado de descarga para su envío a la planta de tratamiento de gas.
Planteo del problema
Una estación compresora de YPF cuenta con dos máquinas que reciben gas a baja presión, cercana a los 4 kg/cm2. Allí, el gas se comprime hasta los 68 kg/cm2 e ingresa a la planta de tratamiento. Si el caudal o la presión de succión del compresor se encuentra por fuera de la ventana operativa, la máquina detiene su funcionamiento para evitar recalentamientos o roturas internas.
En el pasado, se construyó una acometida uniendo un sistema de media presión, cercano a los 8 kg/cm2, con el sistema de baja presión para suplir la disminución de caudal. La estrategia de control original constaba de dos válvulas neumáticas instaladas en cada línea (PV 100A y PV 100B) compartiendo un mismo controlador (PIC 100). La medición de presión y su transmisión se hacía por medio del PIT 100 que se encontraba sobre la línea de succión de los compresores.
Durante los años posteriores, y a medida que el yacimiento se iba desarrollando, el volumen de gas producido a baja presión comenzó a aumentar. Con este nuevo escenario, la conexión entre los dos sistemas se empezó a utilizar solamente para corregir variaciones de presiones ocasionadas por el cierre de pozos productivos. Este proceso en el que se compensa la caída de presión de un sistema con otro es lo que se conoce como “laminación de gas”.
Es necesario notar que la laminación de un gas es una situación no deseable y totalmente ineficiente ya que, como se puede observar, se pierde parte de la energía entregada por los compresores que lograron llevar el gas a un estado de mayor presión.
La problemática se desarrolló en este contexto. A medida que la presión de succión disminuía por el cierre de alguna línea de producción, la laminación resultaba tan abrupta que la presión sobrepasaba los límites establecidos por el fabricante causando el paro del compresor. No se podía sintonizar las velocidades de reacción de las válvulas correctamente. Por ejemplo, la velocidad de la PV 100B de la línea de media presión debía ser más alta que la PV 100A pero, dada la configuración, cualquier cambio en los parámetros del controlador PID afectaría la velocidad de reacción de cada lazo de control. Esta conversión trajo consigo paros repetitivos de compresores ya que no se adecuó de manera correcta el sistema control a la nueva realidad.
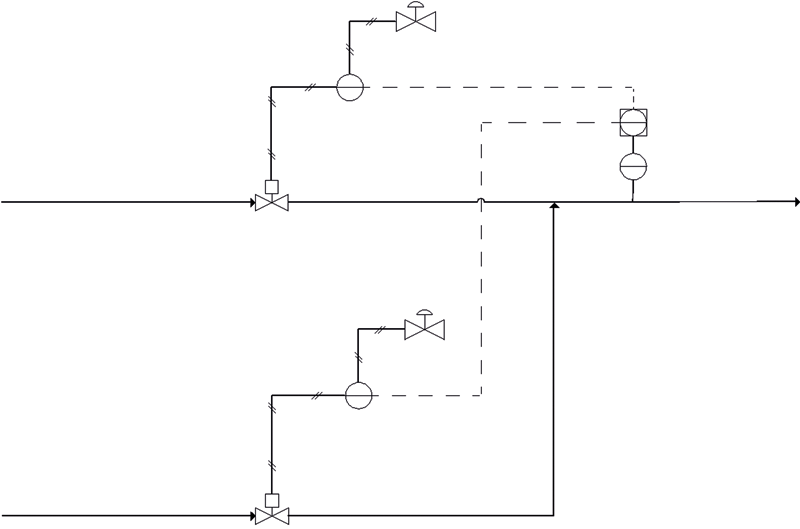
La utilización de Simscape es conveniente ya que, de no contar con la función de transferencia del sistema, permite obtener su modelado en forma gráfica.
Hipótesis
De acuerdo al tipo de sistema, un control de lazo cerrado Feedback es la estrategia de control apropiada para resolver la problemática de regulación de presión por laminación.
No será necesario utilizar la válvula PV 100A para realizar el control del sistema. Esta debe quedar abierta al 100% y en un futuro, quitarla de la instalación.
La válvula PV 100B instalada es de un tamaño mayor al necesario para realizar el control.
Desarrollo del trabajo
Para el desarrollo del trabajo se utiliza la herramienta Simscape que permite crear sistemas físicos dentro del entorno de Simulink. Sus librerías incluyen elementos tales como válvulas, bombas, ductos, resistencias, resortes, transmisiones, intercambiadores de calor, entre otros.
Simscape contiene dos bibliotecas que pertenecen al producto:
- Foundation: contiene elementos físicos básicos y bloques de construcción, así como fuentes y sensores, organizados en sub-bibliotecas de acuerdo con la disciplina técnica y la función realizada.
- Utilities: contiene bloques de entorno esenciales para crear modelos de redes físicas.
De manera orientativa, se detallan los bloques utilizados para realizar el modelo del sistema de gas planteado:
- Solver Configuration: para que los cálculos puedan llevarse a cabo. Se encuentra en la biblioteca Utilities.
- Gas Properties (G): en él se pueden ingresar las propiedades del gas a utilizar en una red de trabajo. Cualquier circuito de gas conectado a este bloque adopta sus parámetros. También es posible tener múltiples circuitos en simulación que usan diferentes gases, pero cada uno de ellos requerirá de su propio bloque de propiedades. El bloque se encuentra en la biblioteca Foundation. Por defecto, el bloque presenta las propiedades del aire seco.
- Reservoir (G): establece condiciones de límite constantes en una red de gas. El volumen de gas dentro del depósito se supone infinito, por lo tanto, casi constante. El fluido sale del reservorio a la presión y temperatura del depósito e ingresa a la presión del depósito, pero su temperatura está determinada por la red de gas aguas arriba. El bloque se encuentra en la biblioteca Foundation. Es necesario especificar el área de la sección transversal del puerto en la entrada. Es posible especificar la presión del yacimiento ingresando un valor, o bien, dejarlo a presión atmosférica.
- Pipe Block (G): modela la dinámica del flujo de la tubería en una red de gas debido a las pérdidas de fricción viscosa y la transferencia de calor por convección entre el gas y la pared de la tubería. Contiene un volumen constante de gas. La presión y la temperatura evolucionan en función de la compresibilidad dinámica y la capacidad térmica de este volumen de gas. El flujo se ahoga cuando en la salida se alcanza la velocidad del sonido. Los puertos A y B son de conservación de gas asociados con la entrada y salida de la tubería. El puerto “H” es el de conservación térmica asociado con la pared de la tubería. Además, hay que ingresar la geometría del ducto: sección transversal, longitud, diámetro hidráulico. Las configuraciones de fricción y transferencia de calor deben mantenerse en los valores predeterminados si la red simulada utiliza tuberías circulares estándar que se colocan en líneas rectas sin curvas. Sin embargo, si la red disponible es más compleja, los parámetros deben modificarse.
- Pressure & Temperature Sensor (G): bloque sensor de presión y temperatura. No hay pérdida de carga ni temperatura en ellos, funcionan como bloques ideales. Se encuentran en la biblioteca Foundation. Este bloque tiene puertos de entrada (“A”) y salida (“B”) y bloques de salida P y T que se pueden conectar al ya conocido Scope para leer los datos medidos.
- Ball Valve (G): modela una válvula de bola en una red de gas. El caudal se basa en el estándar ISO 6358. La válvula está compuesta de una bola esférica en un asiento redondo. El asiento puede ser afilado o cónico. El control de elevación de la válvula se establece mediante el puerto de señal física “L”: cuando es cero, entonces un valor de cero corresponde a la elevación mínima y un valor de uno corresponde a la elevación máxima. El ahogue del gas ocurre cuando la relación de presión a través de la válvula alcanza la relación de presión crítica. No hay intercambio de calor con el medioambiente. Se encuentran en la biblioteca Foundation.
- 2-Way Directional Valve (G): modela una válvula direccional de dos vías en una red de gas. El caudal se basa en la norma ISO 6358. Los puertos A y B son los puertos de conservación de gas. La fracción de apertura de la válvula entre -1 y 1 se establece por el puerto de señal física “S”. Una señal física positiva abre la conexión entre los puertos “A” y “B”. El estrangulamiento ocurre cuando la relación de presión a través de la válvula alcanza la relación de presión crítica. No hay intercambio de calor con el medioambiente. Se encuentran en la biblioteca Foundation.
- Absolute Reference (G): representa la referencia absoluta en una red de gas donde la presión y la temperatura son iguales a cero. Se encuentra en la biblioteca Foundation.
- Perfect Insulator: representa un término en una red térmica sin flujo de calor y sin almacenamiento de energía. Se utiliza como aislamiento para evitar el intercambio de calor con el medioambiente y para modelar un proceso adiabático. Se encuentra en la biblioteca Foundation. En este bloque también se puede establecer un valor inicial y una prioridad para la temperatura en el puerto conectado.
- Constant Volume Chamber (G): modela el almacenamiento de masa y energía en una red de gas. La cámara contiene un volumen constante de gas. La presión y la temperatura evolucionan en función de la compresibilidad dinámica y la capacidad térmica de este volumen de gas. Los puertos “A”, “B”, “C” y “D” son los puertos de conservación de gas asociados con las entradas de la cámara. El puerto “H” es el puerto de conservación térmica asociado con la masa térmica del volumen de gas.
- PS-Simulink Converter: convierte la señal física de entrada en una señal de salida Simulink sin unidades. Se encuentra en la biblioteca Utilities.
- Simulink-PS Converter: convierte una señal de entrada Simulink sin unidades a una señal física. Se encuentra en la biblioteca Utilities.
- Terminator: se utiliza para terminar señales de salida. Su función es prevenir advertencias de simulación por salidas no conectadas.
Modelo del sistema
Un conjunto de pozos se simula utilizando bloques Reservoir (G) a la presión de 4 kg/cm2 y, a la salida de cada uno de ellos, una válvula globo realiza el cierre programado que restringe el paso de caudal de gas. Debido a la operación de los compresores, la repentina merma del ingreso produce una pérdida de presión en el sistema. El gasoducto simulado tiene 500 metros de largo y se encuentra aislado térmicamente. El bloque Constant Volume Chamber (G) se utiliza para el colector de pozos como el scrubber de succión del compresor. En ambos casos: sin intercambio de energía con el exterior.
Cuando la presión en la línea de succión cae por debajo de 4 kg/cm2 (set point), el PID envía una señal a la válvula de control que se encuentra en una cañería con gas a 8 kg/cm2. Al realizar su apertura, se lamina el gas que se dirige a los compresores evitando la detención de las máquinas por baja presión de succión.
Finalmente, un bloque sensor permite ver la evolución de la presión referenciada a una medida absoluta.
Dada la necesidad de mantener constante el proceso de compresión, se propone realizar un control feedback utilizando el PIT 100, la válvula PV 100B y dejando abierta al 100% la PV 100A sin modulación.
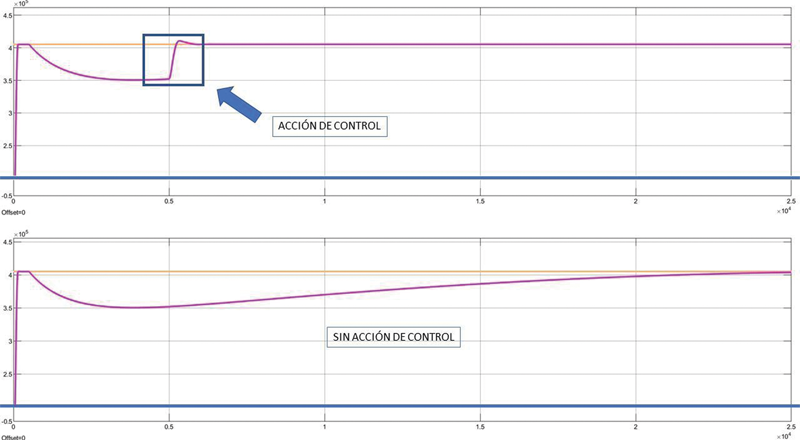
Propuesta de cambio de válvula de control
La apertura de la válvula de control 4” es cercana al 24%. Este es un valor que requiere que todas las fallas que se pueden dar (comunicaciones, atasco de válvula, demora en la carrera, etc.) sean evitadas y, generalmente, esto no se cumple en su totalidad. Se propone utilizar una válvula de 2” de igual porcentaje, lo que genera un valor de 51% de apertura mucho más practicable que el anterior.
Se concluye que el uso del control feedback, con sus parámetros proporcional e integral encontrados, resulta ser la estrategia correcta para evitar la detención de los compresores por baja presión de succión.
Conclusiones
La simulación permite representar el sistema de ductos, sus válvulas y la variación de la presión durante el cierre de los pozos de gas en un subsistema de baja presión.
La utilización de Simscape es conveniente ya que, de no contar con la función de transferencia del sistema, permite obtener su modelado en forma gráfica. Se puede observar el comportamiento del gas metano en el modelo físico.
Tal lo propuesto en la hipótesis de este trabajo, no resulta necesario modular la válvula PV 100A para poder controlar las perturbaciones de presión en el scrubber de succión del compresor, por lo que el controlador PIC 100 solo debe intervenir con la PV 100B y se debe dejar abierta al 100% la PV 100A.
Dada la modulación de la válvula de control que hoy se encuentra en planta, se recomienda cambiarla por una de 2” de tamaño para obtener una mejor reacción del elemento final de control.
Finalmente, se concluye que el uso del control feedback, con sus parámetros proporcional e integral encontrados, resulta ser la estrategia correcta para evitar la detención de los compresores por baja presión de succión, evitando así las pérdidas económicas asociadas.
Acerca de la Especialización
La carrera de Especialización en Automatización Industrial es un posgrado profesional de la Facultad de Ingeniería de la Universidad de Buenos Aires (FIUBA) que se cursa en tres cuatrimestres.
Durante el periodo lectivo 2019-2020 tuvo una implementación particular: por un convenio entre YPF y FIUBA, se dictó para un grupo formado exclusivamente por ingenieros e ingenieras de YPF Upstream. La experiencia resultó muy interesante y productiva, tanto para el personal técnico de YPF como para los docentes e investigadores de FIUBA.
Según el plan de la especialización, después de completar las materias de los tres cuatrimestres, el alumnado debe preparar y defender un trabajo final para obtener su título. El objetivo es integrar lo aprendido con alguna problemática del ambiente laboral en el que se desenvuelve cada estudiante.
Especialización en Automatización Industrial, Facultad de Ingeniería, Universidad de Buenos Aires | www.fi.uba.ar Autor: Carlos Godfrid