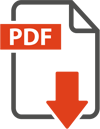
La seguridad de las personas y el ambiente es una de las mayores preocupaciones en la industria de procesos. Plantas de procesos en actividades tan disímiles como química, petroquímica, refinación de petróleo, extracción y explotación de petróleo y gas, minería, tratamiento de metales, etc., han implementado, a lo largo de su historia, diversas soluciones a este problema. Un sistema instrumentado de seguridad es, entonces, un sistema compuesto por sensores, procesadores lógicos y elementos finales cuya función es llevar al proceso a un estado seguro cuando no se cumplen condiciones predeterminadas.
Qué es un Sistema Instrumentado de Seguridad
La agencia Health and Safety Executive (HSE), de Gran Bretaña, define al sistema instrumentado de seguridad como “Un sistema diseñado para responder a condiciones en la planta que pueden ser peligrosas por sí mismas o que, si no se toma ninguna acción podrían, eventualmente, desarrollar una situación peligrosa. Dichos sistemas generan las acciones de salida adecuadas para mitigar consecuencias peligrosas o prevenir el peligro”.
El esquema de la figura 1 define los límites de un sistema instrumentado de seguridad e identifica los dispositivos que pueden formar parte de él. Un sistema instrumentado de seguridad está constituido por un conjunto de dispositivos desde el sensor hasta los elementos finales, incluyendo entradas, salidas, fuente de alimentación y unidades lógicas.
En la norma IEC 61508 de Seguridad Funcional, se define un sistema relacionado con seguridad como aquel que comprende todo lo necesario (equipamiento, programas básicos y de aplicación y elementos humanos) para realizar una o más funciones de seguridad, en donde la falla de la función de seguridad podría dar lugar a un incremento significativo del riesgo para las personas y/o el ambiente.
En la norma de Seguridad Funcional IEC 61511, se define al sistema instrumentado de seguridad como un sistema instrumentado usado para desempeñar una o más funciones instrumentadas de seguridad. Un sistema instrumentado de seguridad se compone de cualquier combinación de sensor(es), unidad(es) lógica(s), y elemento(s) final(es). Esto nos lleva a la definición de función instrumentada de seguridad como una función de seguridad que tiene un nivel de integridad de seguridad especificado necesario para alcanzar una condición de seguridad funcional.
Un sistema instrumentado de seguridad es, entonces, un sistema compuesto por sensores, procesadores lógicos y elementos finales cuya función es llevar al proceso a un estado seguro cuando no se cumplen condiciones predeterminadas.
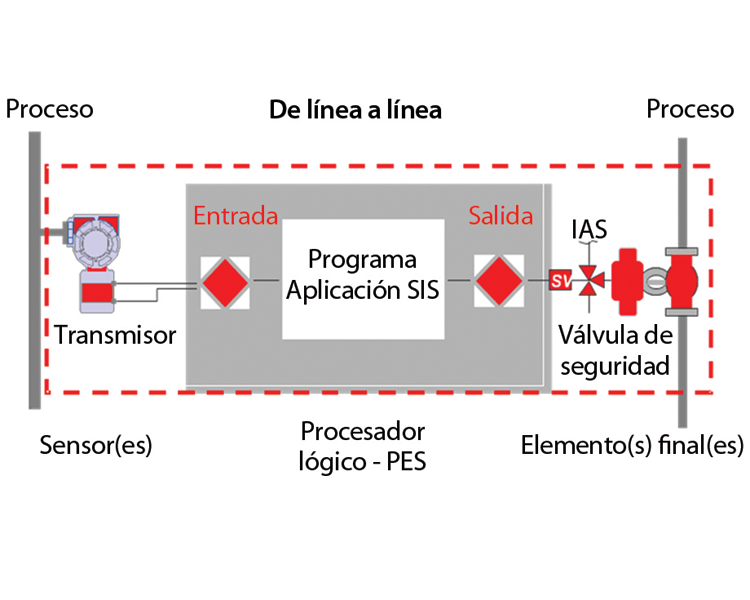
Figura 1. Definición de “sistema instrumentado de seguridad”
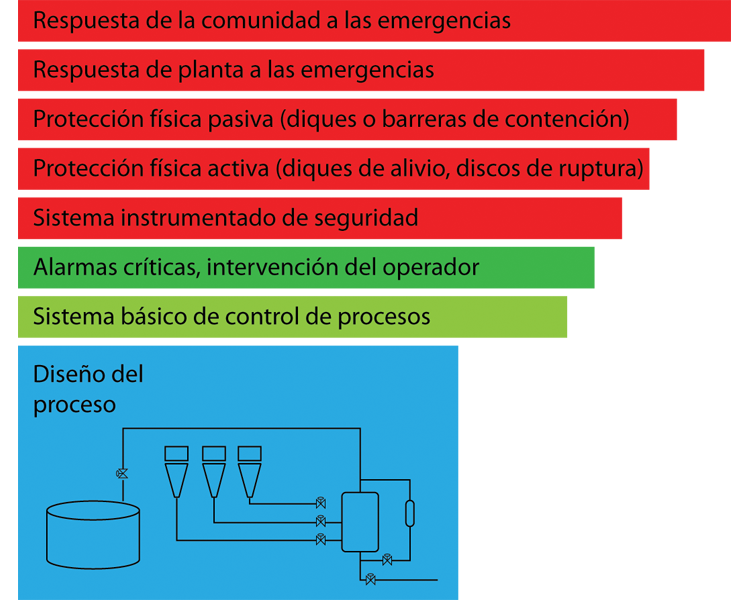
Figura 2. Capas de protección típicas en una planta de procesos moderna.
Niveles de protección
Las plantas de procesos se construyen con múltiples niveles de protección, seleccionados y diseñados para impedir, mitigar y/o reducir las consecuencias de cada uno de los eventos identificados como potencialmente peligrosos.
Dentro de cada proceso existe un número variable de capas de protección que contribuyen a obtener una operación segura. La protección comienza con los elementos fundamentales del diseño del proceso: la selección misma del proceso y del sitio de instalación; la distribución de cada una de las secciones de la planta y los lugares de almacenamiento de productos peligrosos.
Los sistemas de control de proceso constituyen la primera capa protectora de los procesos. Funcionan de manera tal que mantienen las variables de proceso dentro de ciertos valores que se consideran seguros. Sin embargo, el nivel de protección que ofrecen no es suficiente. Es necesario complementarlos con sistemas dedicados e independientes del sistema de control de proceso, por ejemplo, operadores asistidos por sistemas de alarmas.
Los sistemas de seguridad monitorean el estado de las variables y resuelven ecuaciones de estados lógicos del proceso para verificar que se cumplen las condiciones operativas aceptables de la planta. Ante la inminente aparición de condiciones anormales de operación, alertan al operador y, de ser necesario, interrumpen automáticamente las operaciones para evitar la ocurrencia de eventos que, potencialmente, puedan ser riesgosos, no solo para el proceso y la operación, sino también para la seguridad de las personas y el ambiente.
Las capas de mitigación de riesgos, como las que componen los sistemas de detección, alarma y extinción de incendios (fuego y gas), se completan con barreras físicas para contención de líquidos, sistemas de alivio, sistemas de respuesta a emergencias en planta y sistemas de respuesta a emergencias comunitarias. Los sistemas de seguridad monitorean el estado de las variables y resuelven ecuaciones de estados lógicos del proceso para verificar que se cumplen las condiciones operativas aceptables de la planta.
Objetivo de diseño de un sistema instrumentado de seguridad
El objetivo de diseño de los sistemas de seguridad, explicitado desde el inicio mismo del diseño de la planta, es proteger las plantas de proceso durante las fases críticas de la operación: arranque, parada y situaciones de emergencia en general; también deben brindar seguridad durante la operación normal, con el fin de evitar eventos que afecten la operación de la planta, la productividad, la integridad de los equipos de proceso, la seguridad de las personas y el ambiente.
Los sistemas de seguridad bien diseñados cuestan mucho dinero. Pero las pérdidas de producción, costos de reposición y/o reparación de equipos, indemnizaciones al personal de planta y a toda otra persona afectada por un siniestro y la reparación de daños al ambiente debidos a sistemas de seguridad no apropiados, pueden ser mucho mayores que el costo inicial de un sistema bien diseñado y adecuado a las necesidades de la planta. Esto significa que, alarmas inactivas, equipos de seguridad defectuosos y un mantenimiento deficiente del equipamiento de proceso y sus sistemas de protección no son tolerables. Los niveles de confiabilidad de la planta deben ser muy altos.
Sistemas instrumentados de seguridad, ¿cuál elegir?
El sistema de seguridad ideal debe ser capaz de proveer alta confiabilidad, alta disponibilidad y facilitar su mantenimiento, de manera tal que un desperfecto simple, no impida, o inicie, una acción de parada segura no programada.
En los sistemas implementados hace ya muchos años, estos requerimientos fueron difíciles de cumplir. Pero con el transcurso del tiempo, gracias a los progresos en la electrónica y a la experiencia ganada en la investigación de distintos accidentes, se ha mejorado notablemente el diseño, ingeniería e implementación de los sistemas de seguridad.
Además, se ha avanzado en el aspecto normativo a través de la labor de diversos organismos privados, como las normas IEC 61508 y 61511, de la Comisión Electrotécnica Internacional (IEC, por sus siglas en inglés); así como también a través de la gestión de leyes y normas impulsadas por los mismos gobiernos, como OHSAS 1910.119 Act., la Norma Británica para la Gestión de la Seguridad y la Salud Ocupacional (OHSAS, por sus siglas en inglés), y la Sección 304, 1990 “Clean Air Act Ammendments” (“Enmiendas a la Ley de Aire Limpio), en Estados Unidos. Asimismo, a través de la elaboración de prácticas recomendadas como la API 750 “Management of Process Hazards” (“Gestión de riesgos en los procesos”), del Instituto Estadounidense de Petróleo, y las “Guidelines for Safe Automation of Chemical Processes” (“Guías para la automatización segura de procesos químicos”) del Instituto Estadounidense de Ingenieros Químicos (AIChE, por sus siglas en inglés) a través del Centro para la Seguridad de Procesos Químicos (CCPS, por sus siglas en inglés).
Hay que destacar que todas las leyes, normas y prácticas recomendadas incluyen todos los temas que hacen a un sistema de seguridad: diseño, aplicación, documentación, equipamiento, programas de aplicación, test y verificación, entrenamiento del personal y mantenimiento.
La evolución de los sistemas de seguridad, que inicialmente se implementaban con relés, comenzó con la aparición en el mercado de los primeros equipos con electrónica de estado sólido. Su mayor desarrollo llegó a partir del uso de microprocesadores de 32 bits, que permiten la implementación de estrategias de protección complejas que aseguran la integridad de los sistemas de seguridad.
El sistema de seguridad ideal debe ser capaz de proveer alta confiabilidad, alta disponibilidad y facilitar su mantenimiento.
Aplicaciones de sistemas de seguridad
Las industrias de procesos en las que se aplican los sistemas instrumentados de seguridad son las siguientes (la lista no es excluyente):
- Refinerías de petróleo
- Plantas químicas y petroquímicas
- Plataformas costa afuera de explotación de campos de gas y petróleo
- Plantas de explotación de campos de gas y petróleo en tierra
- Sistemas de transporte de petróleo y gas
- Plantas de generación de energía eléctrica
- Operación sin personal de plantas remotas
Algunas aplicaciones típicas incluyen:
- Protección de calderas de generación de vapor y electricidad
- Protección de máquinas rotativas (compresores y turbinas)
- Protección de hornos de proceso
- Encendido y control de quemadores
- Control y protección de reactores químicos
- Control y protección de calderas de recuperación (pulpa y papel)
En cuanto a la complejidad de los sistemas, estos se pueden clasificar como sigue:
- Sistemas de parada de emergencia de unidades de proceso. Corren una lógica simple, son críticos para la seguridad y disponibilidad de la planta. Por ejemplo, los sistemas aplicados a calentadores y bombas de alimentación.
- Sistemas de parada de emergencia para unidades de servicios generales. Ejemplo de esto son las calderas, turbinas y compresores. En general, la lógica de estas unidades es compleja: consiste en muchos pasos y secuencias. Tienen una gran dependencia de funciones de conteo y temporizado.
- Unidades especiales de proceso. Estas unidades tienen una lógica compleja. Su disponibilidad es importante para la disponibilidad de la planta. Ejemplo de esto son las unidades de purificación de hidrógeno.
- Áreas de carga dentro y fuera de la planta. En general, se utilizan sistemas de tipo de enclavamiento de seguridad. Su lógica de parada es moderadamente compleja.
La evolución de los sistemas de seguridad, que inicialmente se implementaban con relés, comenzó con la aparición en el mercado de los primeros equipos con electrónica de estado sólido.
Factores que se deben tener en cuenta para la selección de sistemas instrumentados de seguridad
Para evaluar los sistemas instrumentados de seguridad, se deben considerar, al menos, los siguientes factores:
- Costo de inversión: incluye costos de equipos, programas base y de aplicación, ingeniería, instalación y puesta en marcha.
- Costo de operación: comprende el mantenimiento, soporte por parte del proveedor y partes de repuesto durante la vida útil del sistema.
- Vida útil: la cantidad de años en que se espera que el sistema sea utilizado efectivamente.
- Confiabilidad: la probabilidad de que los componentes del sistema funcionarán apropiadamente durante un periodo dado de años. Esta probabilidad está representada por el tiempo medio entre fallas.
- Flexibilidad: la posibilidad innata del sistema para cambiar o modificar la lógica de parada y expandirla fácilmente.
- Disponibilidad: el porcentaje de tiempo durante el cual el sistema es capaz de realizar la función para la que fue diseñado, durante un periodo dado de tiempo. Es una función de la confiabilidad del sistema.
- Mantener la separación entre el sistema instrumentado de seguridad y el sistema básico de control de procesos: como regla general, las normas exigen dicha separación, promoviendo el uso de múltiples dispositivos o sistemas para segregar las funciones de control de las de seguridad.
Separación de sistemas
Las plantas de procesos emplean sistemas automáticos de control y de seguridad para producir, en forma consistente, productos de calidad, minimizando el trabajo manual del personal de producción, para reducir el error humano cuando se realizan tareas repetitivas, para aumentar la disponibilidad del equipamiento y la eficiencia de la producción y para mejorar la seguridad operacional.
Sistemas básicos de control de procesos
Para el control de procesos, se utilizan instrumentos para la medición de variables, reguladores, unidades de indicación y elementos finales de control. Estos equipos se diseñan, utilizan y mantienen según rutinas preestablecidas, y constituyen el primer nivel de seguridad del proceso.
Hoy en día los sistemas básicos de control de procesos están basados en microprocesadores y se los conoce como sistemas de control distribuido. Son sistemas electrónicos programables modulares compuestos por distintas unidades para el control, visualización y registro de las variables de proceso. Han demostrado ser sumamente confiables, utilizando unidades redundantes en los casos que resulta necesario eliminar fallas de causa común. Una falla simple en un sistema básico de control de procesos se detecta rápidamente, ya que cada módulo corre diagnósticos para la detección de fallas de los componentes, que además se descubren por las características mismas de operación continua del sistema y de la dinámica del proceso. Su característica principal es que son activos, es decir dinámicos. Además, los sistemas de control de procesos deben ser flexibles y así permitir cambios frecuentes. Los parámetros de procesos, es decir, punto de ajuste de control, ajustes de acciones de control, operación manual-automática, etc. requieren cambios. Partes del sistema pueden operar en automático y, otras, en manual.
Sistemas instrumentados de seguridad
Frecuentemente, los dispositivos de medición se instalan en las plantas de procesos para realizar tareas de seguridad. El diseño de los sistemas de seguridad difiere significativamente de los sistemas básicos de control de procesos. Son sistemas que monitorean el estado de variables de procesos consideradas clave en el aspecto seguridad, resuelven ecuaciones lógicas de estado con el objeto de mantener la planta dentro de parámetros operativos aceptables, avisan al operador cuando se están generando condiciones anormales y, cuando es necesario, interrumpen en forma automática las operaciones de la planta para evitar la ocurrencia de eventos que pueden ser potencialmente peligrosos. La característica principal de estos sistemas es que son pasivos, no ejecutan ninguna acción hacia al exterior, a menos que exista una demanda del proceso.
Las normas y prácticas recomendadas requieren que ambos sistemas, el sistema básico de control de procesos y el sistema instrumentado de seguridad, estén separados. No se permiten modificaciones al sistema de seguridad a menos que estén debidamente fundamentadas y sean ejecutadas por personal autorizado, y no por los operadores de planta.
Conclusión
Los sistemas diseñados para control de procesos no son aceptables, en general, para seguridad. La principal razón es que los sistemas de seguridad incluyen autodiagnósticos extensos y dedicados. Esto se debe a que, como el sistema es pasivo, hay fallas que no se autorrevelan, las descubren los diagnósticos. Es necesario indicar que no todos los sistemas basados en microprocesador incluyen el nivel de diagnósticos requeridos por los sistemas de seguridad. La causa es muy simple: costo.
En general, se recomienda que los sistemas de seguridad sean totalmente automáticos y que su accionamiento no dependa de la intervención humana, ya sea operadores o personal de supervisión. La idea rectora es evitar accidentes por errores humanos. Dado que los sistemas instrumentados de seguridad son sistemas pasivos, los operadores deberían entrenar continuamente para saber responder en forma rápida a situaciones de emergencia, ejecutando las acciones correctas para prevenir o mitigar riesgos. Esto, además de ser costoso, dejaría librado al criterio del personal de planta la acción que se debe ejecutar, con lo que se corre el riesgo adicional de no responder a tiempo o de elegir una acción incorrecta, ya sea porque los elementos de juicio no son completos, porque se aprecia erróneamente la situación, porque no se da la importancia adecuada a avisos tempranos o porque, aun con todos los datos en la mano, se toma una decisión errónea.

Por Roberto Varela Autor: Roberto Varela