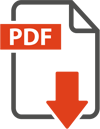
El sistema de control, los drives, el comando y las cuestiones reglamentarias, entre otros El sistema de control Una vez más, atendiendo al hecho de que los recursos de equipamiento disponibles localmente son muy limitados, decidí construir toda la electrónica de control en base a tecnologías convencionales.
Esto significa, concretamente, que toda la lógica de control está basada en tecnología CMOS, y que el procesamiento de señales lo resolví de forma analógica, con amplificadores operacionales.
La mayor parte de las funciones de control las podría haber implementado mediante algún microcontrolador estándar (por ejemplo, Arduino, Raspberry-Pi o similar), pero esta alternativa habría sido más difícil de validar y, sobre todo, más susceptible a problemas de ruido eléctrico. De todas maneras, es evidente que este es el camino a seguir en caso de que se decida construir algún tipo de “prototipo definitivo”.
Una de las unidades desarrolladas es la que se denomina “PSL+L” (“Power Safety Latch & Logic”), que controla el contactor que alimenta las barras de distribución de energía de los motores, y lo desactiva en caso de existir alguna anomalía (por ejemplo, la detección de un impacto o caída accidental del conductor).
Esta unidad también controla la selección de marcha adelante/marcha atrás en forma coordinada con las funciones de giro pivot, que permiten que el ecoPT rote sobre su propio eje vertical, tanto en sentido horario, como antihorario. El giro pivot fue incluido como un ejemplo de “maniobras especiales”.
Además de esta, se podrían desarrollar otras funciones similares en el futuro; una de ellas podría ser “spinning”. La idea detrás de estos “efectos especiales de conducción” es satisfacer la premisa de “conducción divertida”.
La placa PTCU (“Powertrain Control Unit”) recibe el set-point de velocidad desde la palanca de control y genera las señales que se envían a las placas FSESC. Controla, también, las funciones de frenado. Esta unidad incluye los ajustes para las velocidades del giro pivot, los cuales son necesarios para que esta función opere con suavidad.
Tanto la unidad de control de velocidad de los motores (placas FSESC),como la unidad de posicionamiento del mecanismo de dirección se describen más adelante debido a sus características especiales.
También diseñé y construí dos placas periféricas. Una de ellas es la SCU (del inglés, “unidad de control de señalización), la cual comanda todas las luces y señales sonoras, y la CGI (del inglés, “interfaz de pórtico de comando”), cuyo propósito es simplificar las conexiones con el pórtico de comando.
En la tercera versión, adopté niveles lógicos de 12 V (originalmente, eran de 5 V). Esto resolvió algunos problemas menores de ruido eléctrico que existían.
Preví, también, la instalación de un data-logger (“la caja negra”) con cuatro canales analógicos de entrada. Este dispositivo permitirá registrar la velocidad del ecoPT, de la corriente a los motores de tracción, de la corriente producida por el frenado regenerativo y de la generación del panel solar.
Construí las placas de control de manera totalmente “artesanal”, y esto tuvo como consecuencia que aparecieran varios casos de falta de confiabilidad, todos detectados durante la puesta en marcha. Estas fallas, se debían típicamente a falsos contactos o soldaduras frías. Muchos de estos problemas fueron corregidos, pero seguramente debe haber muchos más aún latentes.
Un nuevo comentario 100% práctico: en todas las plaquetas de control, usé leds para indicar visualmente el estado de las señales lógicas. Quizá abusé del recurso y ahora parece un “árbol de Navidad”, pero en la práctica esta información visual fue una ayuda enorme durante las etapas de puesta en marcha.
Los drives
La función de las placas drives es el “simple” control de la velocidad de rotación de los motores de tracción. En el “gremio” de instrumentación y control, se las conoce como “variable frequency drives” (“drives de frecuencia variable”) o simplemente “drives”.
Desde el inicio del proyecto ecoPT, tuve muy claro que estas unidades eran otro de los eslabones críticos y, por lo tanto, hice un análisis bastante pormenorizado de los productos disponibles.
Primero, y solo en función de mis propios antecedentes profesionales, analicé la oferta disponible en el mercado industrial. Todos los productos relevados tenían gran funcionalidad, alto rendimiento, múltiples certificaciones de calidad y excelente documentación. Físicamente, eran productos relativamente grandes y con costos significativos.
Estudié también la disponibilidad de estos productos para el mercado OEM. En este sector, en general, los fabricantes integran estos dispositivos en maquinaria de su propia fabricación.
Todos los productos que analicé eran tipo “board level” y, en términos generales, menos flexibles que los anteriores. Pero hay un detalle muy importante: en algunos casos, la relación de precios llegaba a ser 10:1 entre las soluciones industriales y las OEM.
Por último, analicé lo que podría llamarse “mercado amateur”. Esta es una categoría algo difícil de definir, pero allí se pueden encontrar desde constructores de robots con fines didácticos, hasta entusiastas de los vehículos eléctricos modificados, pasando por pequeños fabricantes de máquinas especiales y constructores de modelos radiocontrolados.
Como era de esperarse, los proveedores que participan de este mercado son muy variados, desde algunos que ofrecen productos de calidad muy dudosa y con documentación muy escasa, hasta otros que parecen haber desarrollado tecnologías interesantes.
No obstante, muchos productos desarrollados para el mercado amateur se hacían atractivos simplemente por tener relaciones de precios de aproximadamente 5:1 con respecto a aquellos para el mercado OEM.
Para el proyecto ecoPT, elegí un drive desarrollado para aplicaciones amateurs. La selección la hice más en base a evidencia circunstancial, que en base a datos duros, pero se puede decir que terminó siendo muy satisfactoria.
No es la idea comparar “perros y gatos”, pero es necesario mencionar que la relación de precios de casi 50:1 que se da entre los productos industriales y los de aficionados es por cosas que esencialmente tienen la misma función. (Esta relación de precios fue decisiva para decidir la selección inicial, ya que si eventualmente la placa no funcionaba, era relativamente poco lo que se perdía.).
Tal vez, esta situación se podría considerar como un buen ejemplo de “low cost automation” (“automatización de bajo costo”), bastante en línea con los conceptos que rondaban en los congresos de IFAC (Federación Internacional de Control Automático, por sus siglas en inglés).
La placa de control que elegí para los motores BLDC (modelo FSESC 4.12) permite operar con corrientes en régimen continuo de 50 A y corrientes de pico de hasta 240 A, ambos valores muy por encima de lo que requieren los motores seleccionados. Este dispositivo utiliza un firmware y un software de interfaz (ambos de tipo fuente abierta) desarrollados por un ingeniero sueco brillante llamado Benjamin Vedder.
Sería muy largo detallar todas las prestaciones y características de las unidades FSESC, pero la más relevante es que operan en base a una tecnología de control vectorial, muy conocida en el sector industrial (“Field Oriented Control”, “control orientado al campo”).
El control vectorial es, indudablemente, el mejor y más eficiente método para la operación de motores BLDC. Esta tecnología fue desarrollada originalmente por investigadores de la Universidad de Darmstadt (Alemania) y de la firma Siemens a fines de los años ‘60, y fue la que abrió el camino para el uso generalizado de los drives de frecuencia variable en el campo industrial.
La configuración de las placas FSESC se simplifica mucho gracias al software de interfaz disponible, el cual es muy intuitivo y flexible. Este programa incluye herramientas para autorreconocimiento de los parámetros eléctricos del motor (resistencia e inductancia de los bobinados, flujo magnético) y algoritmos de auto-tuning para la determinación de los parámetros óptimos de los controladores PID internos. También incluye varias funciones de monitoreo en tiempo real, las cuales son muy útiles para detectar posibles problemas y para optimizar la operación.
Existen también algunos aspectos negativos. Uno de ellos, lo describo con un cierto grado de humor en el punto siguiente.
Otro inconveniente es que el software (tal vez por estar orientado mayormente a usuarios no profesionales) muchas veces denomina ciertos parámetros o funciones con una terminología bastante distinta a la que se utiliza en el ambiente industrial, y esto obliga a decodificar ciertos conceptos. Este proceso requiere de bastante tiempo e incluso puede inducir a errores.
La documentación disponible es escasa y requiere de mejoras.
Algunas cosas que deberían ser extremadamente simples de resolver (como la conexión de un componente periférico) pueden requerir el intercambio de una buena cantidad de correos para aclarar mínimamente los detalles.
Hay muchas opciones y parámetros que se pueden configurar con las placas FSESC, tal vez la más importante es el modo primario de control.
Cuando utilizaba la técnica de dirección diferencial, el modo de control debía garantizar la linealidad entre la señal de entrada y la velocidad de las ruedas, pero cuando cambié por la técnica de ruedas direccionales, configuré esta opción de modo tal que la variable primaria controlada sea la corriente de los motores. Se debe tener en cuenta que el torque erogado por los motores es función directa de esta corriente.
Esta nueva selección tuvo varias consecuencias positivas. Una de ellas fue un arranque suave gracias al alto torque inicial. Esto asegura que el ecoPT comienza a moverse sin dificultad incluso ante la presencia de una pendiente o de un obstáculo.
Otro beneficio indirecto del control en corriente es que actúa como diferencial virtual, asegurando las velocidades correctas de las ruedas de cada lado al girar y, por lo tanto, minimiza el efecto de deslizamiento.
Asociadas a las placas FSESC, desarrollé otras denominadas VMDU (del inglés, “unidad de detección de movimiento del vehículo). Estas unidades utilizan el sensor de efecto Hall integrado en los motores BLDC, y generan dos señales:
- Una salida lógica que detecta si el vehículo está en movimiento
- Una señal analógica o en frecuencia proporcional a la velocidad
Debido a limitaciones de espacio, las VMDU solo las instalé en las ruedas traseras. En el futuro, las salidas de estas unidades serían utilizadas también para implementar un sistema de frenado con función ABS.
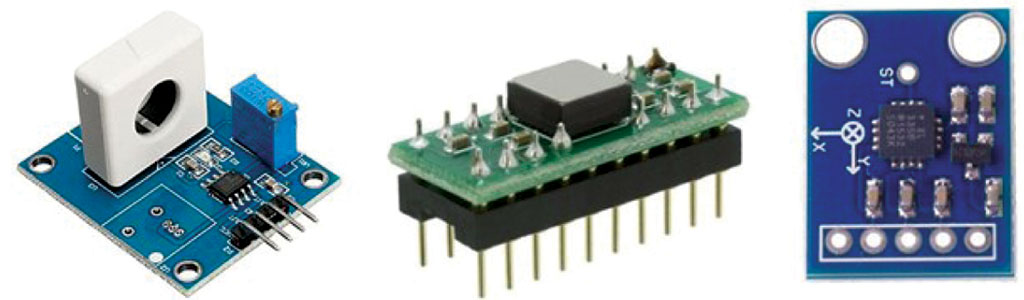
Figura 8. Algunos sensores del ecoPT. Izquierda: sensor de corriente por efecto Hall. Centro: giroscopio MEMS para corrección de virajes. Derecha: acelerómetro de triple eje, para detectar condiciones de impacto.
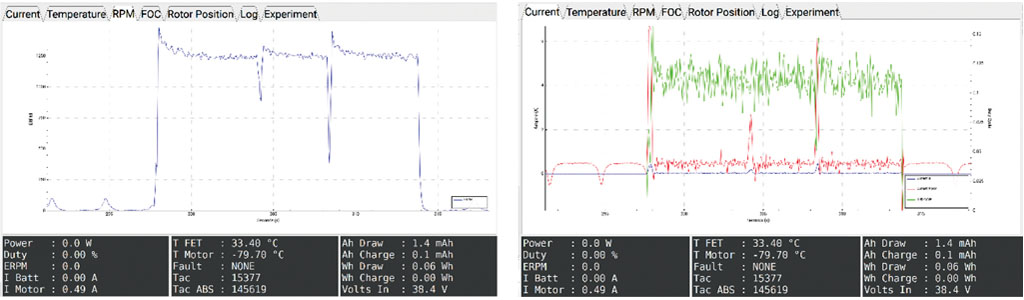
Figura 9. Lazos de control en las unidades FSESC. Izquierda: grafico de ERPM vs. tiempo en modo control de velocidad. La curva muestra la estabilización luego de un salto escalón inicial y luego de dos perturbaciones. Derecha: gráfico de los parámetros eléctricos del motor BLDC en modo de control vectorial. Este ensayo fue realizado en aproximadamente 16% FS (ERPM).
Video 5
La ignorancia siempre es costosa
Las placas FSESC incluyen, indudablemente, muchos detalles técnicos de excelencia, pero con una evidente intención de mantener bajos los costos del hardware, prescindí de todo tipo de protecciones en las entradas y salidas. Esta característica puede generarle serios problemas a quien las utiliza por primera vez.
Durante las primeras etapas de desarrollo del ecoPT, hice varios ensayos para evaluar las placas FSESC, todos sin mayores contratiempos y con resultados satisfactorios. En este momento es posible decir que estuve frente a un claro caso de “suerte de principiante” (ver video 5).
Lamentablemente, cuando comencé a instalar las FSESC en el primer prototipo, la suerte cambió. Durante un periodo de unos quince días, cuatro de estas placas fallaron en forma catastrófica. Hay que decir que esto se debió más a una combinación de improvisación e ignorancia de mi parte que a vicios ocultos de estas unidades.
Hubo todo tipo de errores, desde simples contactos accidentales (la primera placa falló por un toque instantáneo entre la masa del motor y un pack de baterías), hasta reiteradas fallas por falta de entendimiento de las interfases eléctricas.
La placa FSESC está basada en el microcontrolador STM32F-405 que opera con niveles lógicos de 3.3 V y que claramente no admite la menor transgresión de esos valores. Esto significa que, como mínimo, se deben cumplir dos condiciones:
- Nunca una línea de entrada/salida puede recibir un potencial fuera del rango -0,3 a 3,3 V
- Nunca una línea de entrada/salida puede estar activa sin que el microcontrolador esté energizado
El problema era que el diseño original violaba ambas condiciones, debido a que toda la lógica funcionaba con 5 V y que, además, todas las unidades de control recibían tensión antes de que recibieran energía las placas FSESC.
Afortunadamente la solución fue muy simple. Solo bastó con incorporar un par de dispositivos aisladores de señal entre las placas de control y las FSESC, alimentados desde una salida auxiliar de las propias FSESC. En la práctica, esto lo materialicé solamente con seguidores de tensión.
Ahora que ya ha sido explicada, toda esta secuencia de eventos parece muy sencilla; pero en la realidad, todo esto fue una de las etapas más frustrantes del proyecto. Aquí la moraleja es bastante clara y simple: la improvisación combinada con ignorancia siempre es muy costosa.
El pórtico de comando
El pórtico de comando cumple una doble función:
- Lugar de montaje de todos los elementos de comando y medición
- Estructura desde la cual el conductor se sostiene mientras conduce.
En el caso del prototipo que desarrollé, el diseño del pórtico de comando estuvo fuertemente condicionado por las posibilidades locales de fabricación.
La base del diseño es la palanca de control, la cual posee tres funciones:
- Control de velocidad de avance o retroceso
- Accionamiento de los frenos, incluido el freno de estacionamiento
- Control de dirección
La operación de la palanca de control requiere cierta habilidad manual por parte del conductor, ya que comanda, tanto la velocidad, como la dirección del vehículo. Esto podría, inclusive, ser considerado como una debilidad del diseño, ya que cuando se encuentra alguna irregularidad en el camino (por ejemplo, un bache o una loma), se pueden producir movimientos involuntarios en la mano del conductor, los que a su vez podrían producir cambios erráticos en la dirección del vehículo.
Existen varias posibilidades para minimizar este efecto, una de ellas fue el desarrollo de la YCU (unidad de compensación de virajes, por sus siglas en inglés), como se verá más adelante.
En el pórtico de comando también se ubica el pulsador que permite seleccionar las marchas adelante/atrás (*) y los pulsadores que controlan las maniobras especiales. Una alarma sonora clásica de retroceso indica el estado de la selección. Un multímetro eléctrico (tensión y corriente de batería, potencia erogada, estimación de autonomía, etc.) y un computador GPS de velocidad y distancia completan el esquema.
La vinculación eléctrica entre la electrónica de control y el pórtico de comando, la hice mediante tres cables múltiples (3 x 6 conductores cada uno) que incluyen conectores M16 para facilitar un desarme rápido. En el futuro, este enlace se podría resolver con CAN Bus (solo tres conductores).
Un cambio estratégico: de dirección diferencial a ruedas direccionales
Según lo que expliqué más arriba, tanto en la primera, como en la segunda versión, utilicé la técnica de dirección diferencial, y aunque se pueda considerar como “cambiar de caballo en el medio del río”, a fines de 2020, decidí migrar a un esquema de ruedas frontales servoposicionadas, decisión respaldada por las razones que ya mencioné antes.
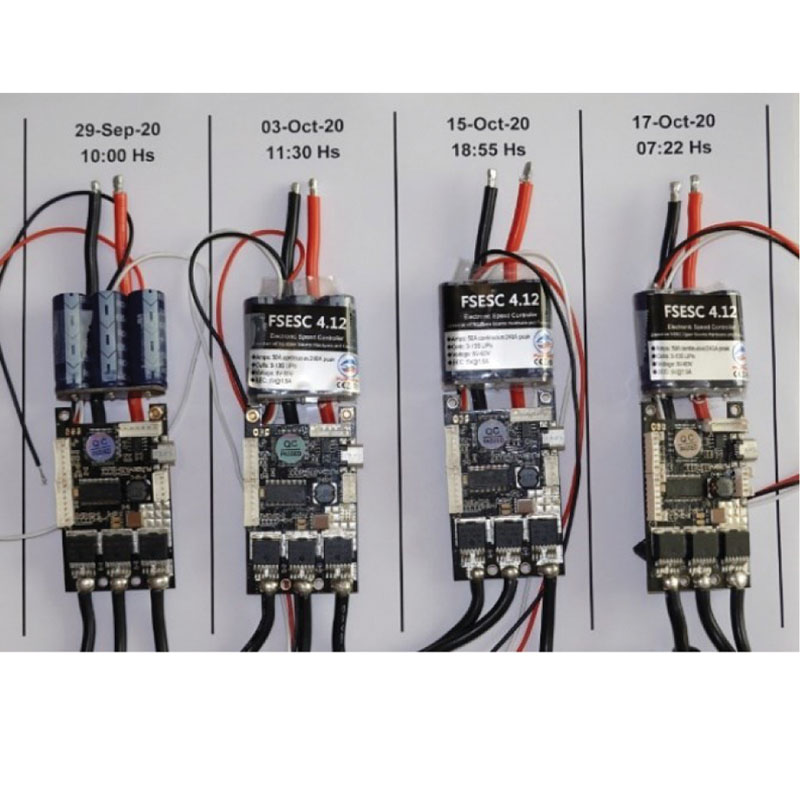
Figura 10. Una imagen triste. Estas son las cuatro placas FSESC que fueron “brutalmente asesinadas” durante la puesta en marcha de la primera versión del ecoPT. El móvil del crimen fue muy simple: una inoportuna combinación de improvisación e ignorancia.
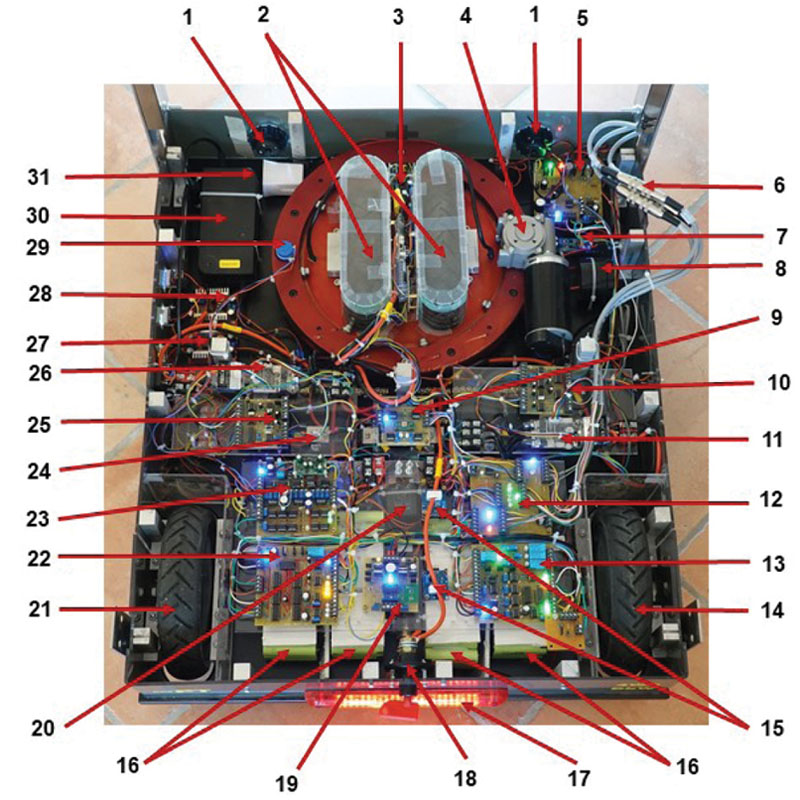
Figura 11. Componentes eléctricos y electrónicos. 1. Faroles led frontales | 2. Motores de tracción frontales | 3. Drives FSESC y placas de interfaz frontales | 4. Servomotor de dirección | 5. Unidad de control de luces y alarmas (SCU) | 6. Conectores M16 para cables del pórtico de comando | 7. Fuente switching para la SCU (12 V) | 8. Alarma de retroceso | 9. Unidad de compensación de viraje (YCU) | 10. Unidad de detección de movimiento del vehículo | 11 Drive FSESC trasero-derecho | 12. Unidad de interfaz con el pórtico de comando | 13. Unidad de control de tracción (PTCU) | 14. Motor de tracción trasero-derecho | 15. Sensores de corriente por efecto Hall | 16. Conjuntos de baterías de ion-litio (10 S/3 P) | 17. Luz de posición trasera más luz de freno | 18. Interruptor maestro accionado con llave | 19. Placa de PWM y puente-H-para servomotor | 20. Contactor de alimentación de motores | 21. Motor de tracción trasero-izquierdo | 22. Unidad de enclavamiento y lógica (PSLLU) | 23. Unidad de control de la servodirección (SSU) | 24. Resistores shunt para la medición de la corriente | 25. Unidad de detección de movimiento del vehículo (VMDU) | 26. Drive FSESC trasero-Izquierdo | 27. Placa elevadora de tensión para entrada auxiliar de 12 V | 28. Placa elevadora de tensión para el panel solar | 29. Realimentación de posición para servo de dirección | 30. Cargador de baterías (220/240 V) | 31 Bocina
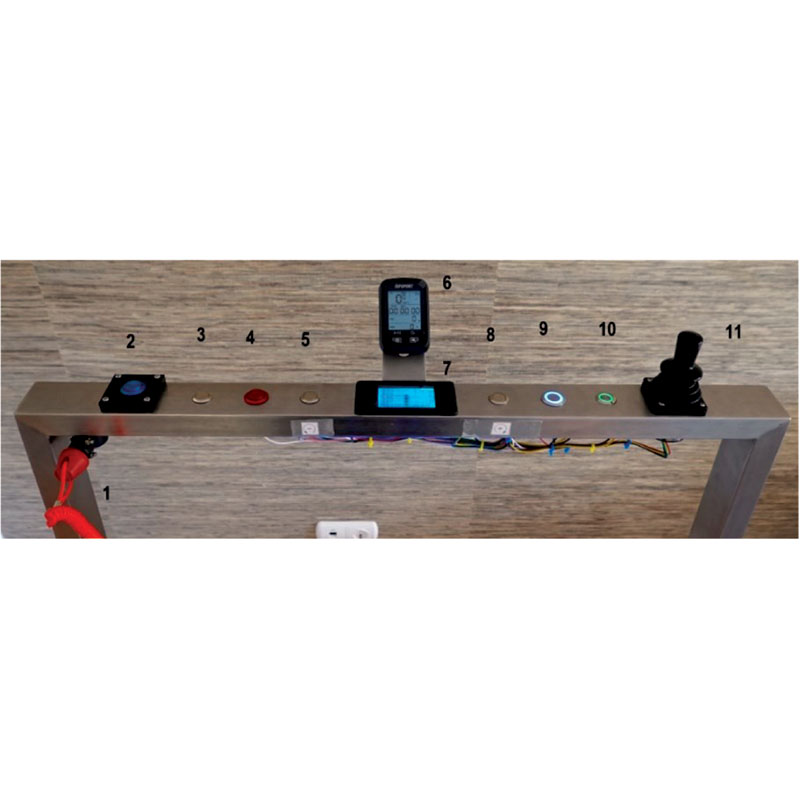
Figura 12. Pórtico de comando. 1. Interruptor de “hombre muerto” | 2. Pulsador marcha adelante/marcha atrás | 3. Bocina | 4. Corte de alimentación eléctrica a los motores | 5. Giro pivot (sentido antihorario) | 6. Velocímetro/odómetro GPS | 7. Multimedidor V + I + P + autonomía | 8. Giro pivot (sentido horario) | 9. Alimentación de motores más leds de estado | 10. Faros frontales y luz roja de posición | 11. Palanca de control de velocidad y dirección
Un cambio estratégico: de dirección diferencial a ruedas direccionales
Según lo que expliqué más arriba, tanto en la primera, como en la segunda versión, utilicé la técnica de dirección diferencial, y aunque se pueda considerar como “cambiar de caballo en el medio del río”, a fines de 2020, decidí migrar a un esquema de ruedas frontales servoposicionadas, decisión respaldada por las razones que ya mencioné antes.
El conjunto de dirección que diseñé difiere mucho de otras alternativas disponibles. Está estructurado a partir de un engranaje plano de dientes rectos (300 mm de distancia) sobre el cual se monta el tándem de motores de tracción, en cuyo espacio intermedio se ubican las placas de control (FSESC) e interfaz.
El mencionado engranaje, a su vez, está montado entre dos aros de aluminio de calidad aeronáutica (aleación 7075 T6, distancia de 368 mm), que conforman la estructura principal del conjunto.
La fuerza axial (por ejemplo, peso del vehículo más peso del conductor) se toma mediante un conjunto de dieciséis minirrodamientos de bolillas montados en las caras internas de los aros. Entre los aros, también ubiqué cuatro engranajes (30 mm) cuya función es centrar el engranaje del plano principal.
Tanto el servomotor como el potenciómetro multivuelta de precisión para realimentación de posición están montados sobre el aro superior. El servomotor también incluye un encoder digital que se puede usar como sensor alternativo de realimentación de posición.
Todas las piezas de aluminio fueron anodizadas en color rojo a los efectos de lograr el pasivado de las superficies. El conjunto fue calibrado para operar en el rango de -45 a 45°, que es el que se utiliza para las funciones normales de dirección y, además, se puede forzar a posiciones extremas de -90 o 90° para las funciones de giro pivot. El límite de 90° también es utilizado por el freno de estacionamiento.
El servomotor que seleccioné es de “calidad comercial” y es un producto normalmente destinado al accionamiento de puertas automáticas. Es un motor convencional con escobillas, con una potencia nominal de 100 W (24 V). La velocidad de salida de su caja reductora es de 220 rpm. Considerando esa velocidad y la relación adicional de desmultiplicación que introducen los engranajes de la unidad, se tiene un tiempo total de accionamiento de aproximadamente 0,68 segundos para la excursión de -45 a 45°, tiempo que probó ser ampliamente satisfactorio.
El posicionamiento del servomotor se efectúa mediante una placa denominada SSU (unidad de posicionamiento de la dirección servoperada, por sus siglas en inglés). La primera versión de la placa SSU la diseñé y construí en base a una estrategia de control que podría ser denominada “on-off con banda muerta ajustable”. La sencillez y la velocidad de construcción fueron determinantes para tomar esta decisión.
La SSU inicial operaba en forma satisfactoria, pero durante los ensayos en calles se hizo notorio que era necesario fijar la banda muerta en un mínimo de ±3% para que no oscilara el servomecanismo. Este valor, a su vez, se traducía en un “ángulo muerto” del servomecanismo de aproximadamente ±3°.
En la práctica, este valor se hizo muy peligroso ya que, si eventualmente el servo había quedado posicionado en uno de los extremos de la banda muerta, y el conductor manipulaba la palanca de control en la dirección contraria, el servomecanismo excursionaba bruscamente unos 6° con la consiguiente desestabilización del vehículo. Inclusive a velocidades muy moderadas (6 a 8 km/h) esta respuesta era inaceptable.
En base a estos resultados experimentales, decidí construir una nueva versión de la placa SSU utilizando el clásico modo de control PID. La etapa de entrada incluye los acondicionadores de señal y un amplificador diferencial para calcular la señal de error.
Implementé el algoritmo PID con un circuito tradicional basado en amplificadores operacionales. Cada modo de control cuenta con cuatro rangos seleccionables. La etapa de salida incluye un separador de señal para convertir los niveles internos bipolares en salidas de 0 a 5 V, y también incluye los límites de carrera ajustables. Una simple lógica permite forzar las posiciones del servomecanismo en los valores extremos de -90 y 90°. Una placa auxiliar convierte las salidas analógicas de control a pulsos mediante dos circuitos PWM, e incluye un puente H estructurado con MOSFET para la alimentación del servomotor.
Esta nueva versión de la placa SSU se comportó increíblemente bien desde el inicio, brindando un ajuste rápido, estable y preciso del servomecanismo de dirección.
La solución adoptada con ruedas direccionales tiene, además, otras dos características interesantes:
- Compatibilidad con las funciones de giro pivot
- Posibilidad de trabar las ruedas frontales en la posición 90°, lo que resulta en un simple freno de estacionamiento que no requiere energía de mantenimiento.
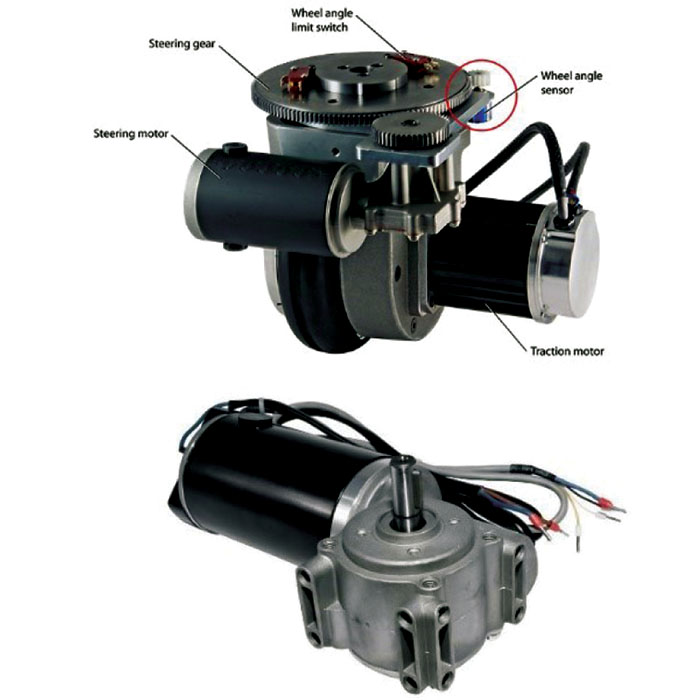
Figura 13. Dirección servoperada. Arriba: típica unidad de tracción y dirección como la que se emplea en algunos vehículos robóticos. El conjunto de la imagen pertenece a la empresa Allied Motion, de Estados Unidos. Abajo: motor seleccionado para el conjunto servoperado de dirección, que se utiliza normalmente en puertas operadas automáticamente.
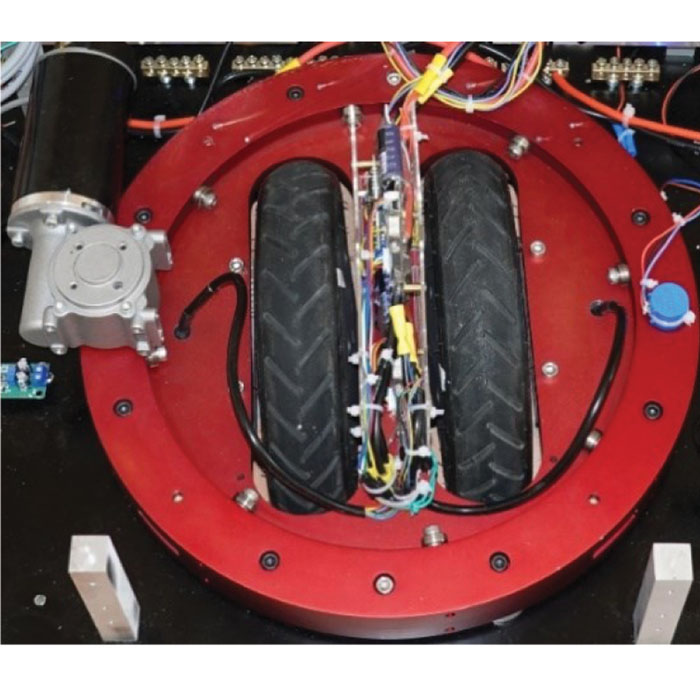
Figura 14. Conjunto de dirección electrónica servoperada. Vista del nuevo conjunto de dirección ya instalado en la plataforma inferior del ecoPT. En el centro se ubican los dos motores de tracción junto a la correspondiente electrónica de control. A la izquierda se observa el servomotor. La pieza azul que se aprecia a la derecha es el potenciómetro multivuelta para realimentación de posición.

Figura 15. “Orgía” analógica. Este es el sobrenombre que se le dio a la nueva placa SSU que controla el posicionamiento del servomecanismo. Es tecnología clásica de inicios de los años ‘80, pero en la práctica se ha comportado muy eficientemente. Incluye quince amplificadores operacionales (CA-3140), tres DIP switches, cuatro interruptores analógicos SPDT (DG-419), dieciséis trimpots, un relay y el conjunto de fuentes ±12 y +5 V para referencias. La alimentación general es de 24 V.
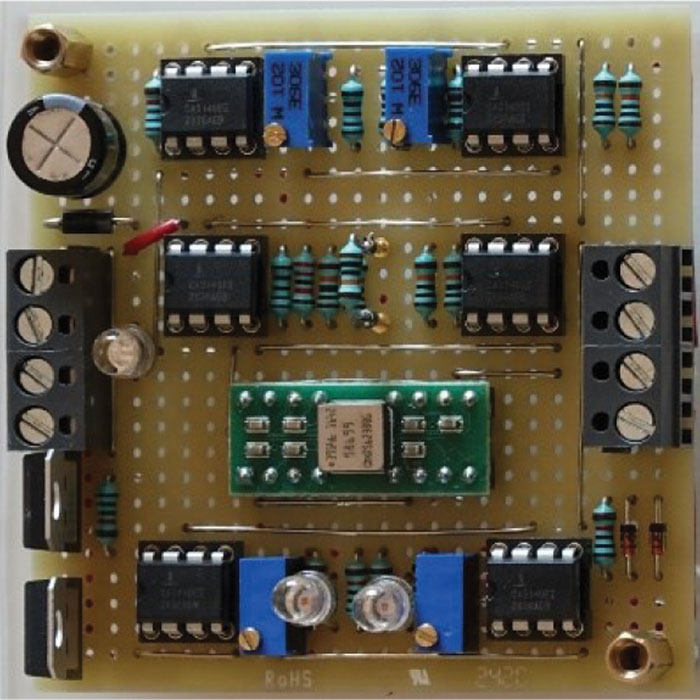
Figura 16. Placa YCU. En la parte superior, los circuitos integrados requeridos para implementar las interfases y para el ajuste de ganancia. El sensor ADXRS-623 es el pequeño cuadrado plateado. Este componente tiene terminales con tecnología “Ceramic Ball Grid Array”, que lo hace totalmente inutilizable por un desarrollista amateur. Afortunadamente, también está disponible montado en una pequeña plaqueta, como se observa en la imagen.
Compensación de viraje
Ya mencioné que un movimiento no intencional de la mano del conductor puede resultar en un cambio brusco en la trayectoria del ecoPT. En realidad, esta perturbación también puede ser consecuencia de algún obstáculo encontrado en el camino o de un cambio en el agarre de las ruedas al piso (por ejemplo, la clásica situación de tener dos ruedas en un camino asfaltado y las otras dos sobre pasto).
Muchos automóviles modernos enfrentan estos efectos con sistemas que tienen denominaciones tales como “control activo de viraje”, “programa de estabilidad electrónica” (ESP), y similares.
La placa SSU descripta incluye el modo de control derivativo, el cual puede ser útil para compensar perturbaciones introducidas por la mano del conductor, pero no puede reaccionar ante otras interferencias. Entonces, diseñé y construí un módulo denominado “YCU” (“unidad de compensación de viraje”), que en la práctica funciona como un modo derivativo virtual. La siguiente fórmula intenta explicar el concepto:
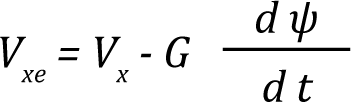
en donde “Vxe” es la entrada efectiva a la placa SSU; “Vx”, el set-point de dirección; “G”, el factor de ganancia ajustable; “dψ/d t”, la velocidad de viraje (°/s).
La acción introducida por la YCU simplemente consiste en sumar un término que depende de la velocidad de viraje del vehículo al set-point originado en la palanca de control, o sea, la trayectoria solicitada por el conductor.
Los giros en sentido horario son positivos y los antihorarios, negativos. De esta manera el set-point de dirección se corrige en la fuente, antes de ser ingresado en la unidad SSU.
La electrónica que desarrollé se basa en el sensor giroscópico ADXRS-623, el cual está basado en tecnología MEMS y entrega una salida que a velocidad de giro nula está en el 50% de la escala, y varía proporcionalmente a dicha velocidad.
El sensor lo instalé en el centro de la plataforma inferior en una posición que intenta estar alineada con el eje vertical del conductor.
La placa YCU ya fue ensayada en condiciones de campo con resultados satisfactorios. No obstante, se estima que aún se requiere un cierto grado de optimización.
El sensor giroscópico tiene una alta relación de rechazo a aceleraciones en los otros ejes; no obstante, se han notado algunas interacciones no deseadas cuando el ecoPT “choca” con alguna irregularidad mayor del camino. Es precisamente este efecto el que debe mejorar, y es muy probable que esto se pueda lograr mediante el ajuste del ancho de banda.
Una vez más, una observación práctica: durante los ensayos en calles de la YCU, puede no ser fácil interpretar las correcciones que introduce el llamado “efecto de control”. Esto se podría ver con instrumental adecuado, pero esta solución es compleja y no está disponible en este desarrollo. Entonces, la YCU la construí incluyendo dos simples comparadores que detectan cuando la intervención de la YCU supera un cierto umbral. Estas salidas, luego se convierten en un “beep” en la SCU, y este sonido le brinda al conductor una clara señal acerca de la intervención de la YCU.
Algunas consideraciones reglamentarias
Al presente, no tengo una idea clara acerca de cómo sería el “encuadramiento legal” del ecoPT, si es que alguna vez fuera a circular “oficialmente” por la vía pública.
Los monopatines eléctricos no requieren ningún tipo de licencia ni edad mínima, aunque algunos países o regiones fijan un mínimo de dieciséis años.
Estos vehículos, en general, están limitados a una potencia máxima de 250 W. En Europa (particularmente en Alemania) hay reglamentaciones que cubren a los llamados “PedElecs” (básicamente, bicicletas que tienen un motor eléctrico de asistencia), pero están también limitadas a 250 W, y el motor solo puede funcionar cuando el usuario tiene los pies ubicados sobre los pedales.
Tampoco estudié las reglamentaciones en base a las cuales se diseñó el segway, ni las certificaciones que posee, pero es notorio que para conducirlo es obligatorio utilizar casco.
Con respecto a las sillas de ruedas eléctricas y los triciclos de cortesía (los que típicamente se pueden encontrar en algunos centros comerciales) es muy probable que tengan encuadramientos tipo “uso profesional” (o alguna calificación similar) y, por lo tanto, las reglamentaciones son mucho más permisivas, fundamentalmente en cuanto a potencia o permisos de uso.
De todas maneras, todos estos vehículos (y esto sería “sin excepción”) están limitados a una velocidad máxima de 25 km/hr. A pesar de esto, es frecuente observar vehículos eléctricos modificados que pueden viajar mucho más rápido que ese límite. Es habitual, incluso, verlos transitando por rutas nacionales.
Finalmente, se puede decir que es casi seguro que este tipo de vehículo deba cumplir con los lineamientos de la Norma IEC (EN) 61000 respecto a compatibilidad electromagnética y de la Norma UNECE R-100 respecto al tema de seguridad de baterías de ion-litio o similares. Sometí el ecoPT a muchas horas de ensayos transitando en la vía pública, en superficies tales como veredas, bicisendas, pasarelas, calles y avenidas. En términos generales, se puede decir que se comporta según lo previsto, y en algunos aspectos incluso mejor. No obstante, hay algunos detalles del diseño y de la construcción que deberían ser objeto de mejora en caso de que se decida elaborar un prototipo avanzado.
- Cuando hice el diseño mecánico, una de las ideas fue lograr que las ruedas no sean fácilmente visibles. El objetivo era dar la impresión de que la plataforma inferior estaba “flotando en el aire”. Para lograr esto, básicamente mantuve muy bajo el despeje respecto al piso. Ese valor, actualmente, es de unos 85 mm. Lamentablemente, por esta característica, es frecuente que la plataforma inferior toque el piso ante una irregularidad del camino (por ejemplo, una canaleta o un montículo). Claramente, esta dimensión se debería incrementar unos 40 o 50 mm, pero esto a su vez podría degradar algo la estabilidad del vehículo, o sea que es un cambio que se debe introducir con precauciones. El bajo despeje también implica que la circulación “off-road” está descartada, al menos por el momento.
- Mencioné varias veces que la palanca de control es un comando multifunción que controla la velocidad de avance, la intensidad de frenado y la dirección del vehículo. Si bien esto parece ser una buena elección, ya que se ahorra componentes, también está claro que esta característica hace que se requiera una cierta habilidad manual por parte del conductor y que pueda ser fuente de algún problema cuando se conduce a una velocidad algo elevada y se encuentra una irregularidad del camino, con el consiguiente movimiento involuntario de la mano del conductor. En la práctica, ya consideré esta situación con el desarrollo de la YCU, no obstante, se podrían también imaginar otras alternativas, como las siguientes:
- Rediseño de la estructura de comandos con separación de las funciones de control de velocidad y control de dirección.
- Introducción de algún tipo de función de caracterización entre la salida de la palanca de control y la entrada de la SSU en forma análoga a lo que hacen los sistemas de dirección progresiva (a veces también llamados “dirección activa”). Esta función, básicamente, debería tener baja ganancia en la zona de reposo de la palanca de control, y luego aumentar dicha ganancia a medida que la palanca de control se aleja del centro.
- Uso de una palanca de control mucho más robusta, de “calidad industrial”.
- Combinación de todas las opciones mencionadas.
- Hay mucho por reconsiderar respecto del pórtico de comando, en particular en lo referido a su estética y ergonomía. La primera debe ser mejorada para lograr una imagen más moderna y funcional; la segunda, para incluir como mínimo una buena manija de sujeción para el conductor.
- El ecoPT no incluye ningún tipo de mecanismo de suspensión. Para absorber las irregularidades del camino, solo dispone de la flexibilidad de las ruedas de goma. Si consideramos que el peso total es significativo (ecoPT más conductor), esto resulta en un andar bastante rústico y es entonces que la mayoría de las irregularidades del camino terminan siendo absorbidas por la espalda del conductor y, por lo tanto, la conducción por periodos prolongados (digamos mayor a dos o tres horas) puede ser bastante cansadora. El eventual agregado de algún tipo de suspensión no es algo simple de realizar y se debe analizar junto a otra opción: el uso de cubiertas sólidas a los efectos de evitar pinchaduras.
- Cuando decidí cambiar el método de dirección diferencial por el método de ruedas direccionales, realmente la geometría del ecoPT comenzó a parecerse más a la de un triciclo (¡aunque con ruedas tractoras en tándem en la parte delantera!) que a un vehículo clásico de cuatro ruedas. Además, este cambio trajo aparejada una ligera reducción (del orden del 10 %) en la distancia entre ejes. Estas modificaciones tuvieron como consecuencia que el ecoPT se comportara en forma algo más inestable en giros cerrados y en frenadas bruscas. Para compensar en parte esta situación, luego de varios ensayos con la tercera versión, decidí instalar dos ruedas giratorias auxiliares en las esquinas frontales. De todas maneras, esto se debe entender como un paliativo más que como una solución definitiva. Una posibilidad sería aumentar la distancia entre ejes (lo que necesariamente significaría alargar las plataformas) y otra sería volver a un esquema de “base cuadrada” como el que empleé en la segunda versión, pero utilizando ruedas servodireccionales con una suerte de geometría Ackermann modificada.
- Tanto las placas FSESC, como las fuentes switching, son bastante ruidosas desde un punto de vista eléctrico. Este efecto se hace notorio, por ejemplo, en el instante en que terminan de botearse las placas FSESC cada vez que se energizan. Actualmente, no existe ningún inconveniente derivado de estas características, pero seguramente debería ser un tema para estudiar en el futuro.
- Se pueden imaginar buena cantidad de soluciones personalizadas a fin de que el ecoPT pueda cubrir diferentes necesidades. Por ejemplo, sería muy simple modificar la plataforma superior para generar un espacio de guardado. Otra posibilidad sería incluir algún tipo de “apoya cola” similar a los que se utilizan en algunas atracciones de Disney World.
- Y por último, y de gran importancia, habría que estudiar el reemplazo de toda la electrónica convencional desarrollada por algún microcontrolador dedicado o, como mínimo, por alguna plataforma computacional estándar (por ejemplo, Arduino o similar). Este cambio también debería implicar el uso de algún tipo de bus de comunicaciones (por ejemplo, CAN Bus) entre la unidad de control y el pórtico de comando. Obviamente, esta modificación también tendría que incluir a la función de BMS, para la cual se ha reservado el espacio físico, pero que no ha sido instalada. Un nuevo tipo de electrónica de control, también debería permitir diversificar las maniobras especiales de conducción (hasta ahora, solo se ha implementado el giro pivot) y el desarrollo de otras características como ser la función “Sígame”, que permita que el ecoPT siga a su dueño (¡como un perro obediente!) en lugares muy concurridos o en zonas en donde no está permitido utilizar un vehículo. El cambio de la plataforma de control sería muy relevante y seguramente tendría un costo de desarrollo significativo. A esto debe sumarse que es muy probable que los tiempos de realización sean algo impredecibles.
Al presente, fui yo quien condujo durante prácticamente todos los ensayos realizados. Si en algún momento se hicieran pruebas de conducción con terceros, seguramente aparecerían muchos problemas más. Pero, con los aquí listados es suficiente.
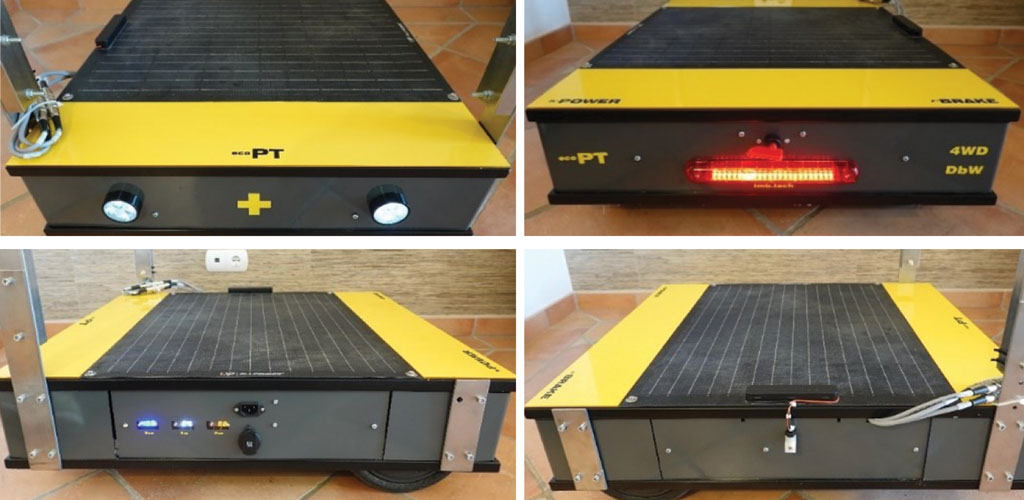
Figura 17. Vistas de los cuatro laterales. Imágenes del ecoPT según construcción. Las fotos superiores muestran los paneles frontal y trasero. La imagen inferior izquierda es del lateral que incluye las conexiones eléctricas para 220/240 Vca y para 12 Vcc (encendedor de automóvil). También se observan los voltímetros auxiliares para la medición de la tensión de baterías y de las tensiones de carga vinculadas con el panel solar o con la entrada auxiliar de 12 Vcc. La imagen inferior derecha muestra el lateral donde se conecta el panel solar mediante un conector DIN 43650 Tipo C.
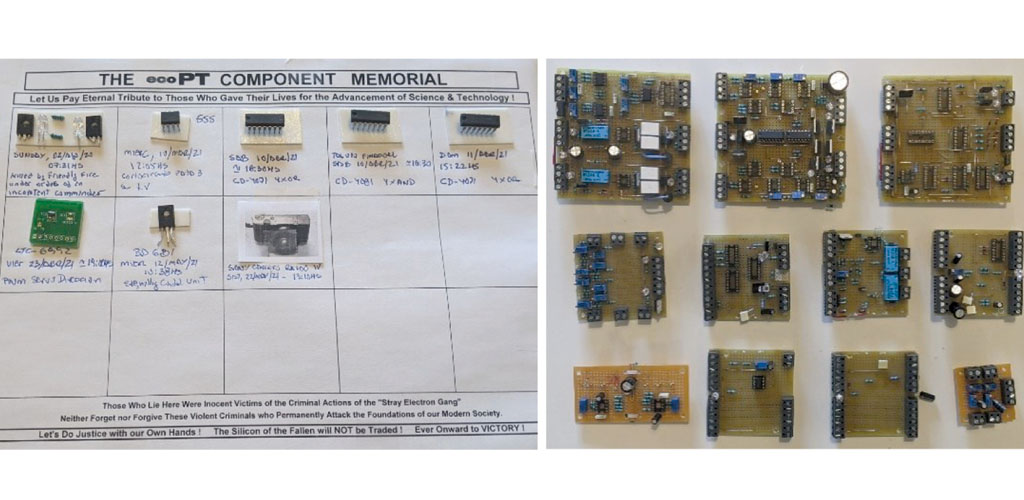
Figura 18. Detrás de escena. Izquierda: caídos en combate. Derecha: las rechazadas (placas diseñadas, construidas y ensayadas; y luego reemplazadas)
Conclusiones
Como dije en el comienzo, el proyecto ecoPT nació a partir de una idea totalmente fortuita y sirvió de entretenimiento tecnológico durante la crisis mundial CoViD.
Es importante recalcar que al inicio de todo este proceso, tenía poco o nulo conocimiento acerca de vehículos eléctricos. Esto se hace bastante evidente analizando las decisiones de diseño erradas y los múltiples errores cometidos a lo largo del proyecto.
Pero este desarrollo también pone en evidencia el enorme poder de las fuentes públicas de información disponibles actualmente que ayudan a mitigar (en parte) la mencionada falta de conocimiento.
Todo este proyecto lo hice con recursos limitados, en particular en lo referido a espacio y equipamiento de trabajo. Esta realidad condicionó varias decisiones de diseño. De hecho, no podría ser calificado como “invento de garage” simplemente porque no hubo un garage disponible.
El ecoPT podría parecer cavernícola frente al despliegue técnico que hacen algunos vehículos eléctricos disponibles (sin ir muy lejos, se podría mencionar al segway), pero la realidad es que este desarrollo parece ser único en el mundo en, como mínimo, dos aspectos. El primero es que, gracias al panel solar, es 100% autosuficiente desde un punto de vista energético, en otras palabras, para funcionar nunca necesitaría conectarse a una fuente externa de energía.
Estimé que, si el ecoPT se utiliza diariamente en condiciones moderadas (por ejemplo, velocidad en el rango de 10 a 15 km/h, con un conductor de no más de 75 kg de peso y por superficies llanas) durante un periodo de no más de una o dos horas, y que si, además, se lo mantiene bajo irradiación solar un mínimo de seis a ocho horas, la energía generada podría alcanzar con comodidad para compensar la energía consumida.
El segundo aspecto que haría del ecoPT único en el mundo es la combinación del concepto “Drive by Wire” con el hecho que posee tracción permanente en las cuatro ruedas, sumado a la capacidad de efectuar maniobras especiales que en el prototipo desarrollado están limitadas al giro pivot, pero que con el desarrollo de un sistema de control más sofisticado podrían estar solo limitadas por la imaginación.
Como dije, hice todo este desarrollo sin ningún objetivo comercial. No obstante, en caso de que en un futuro se pueda considerar el ecoPT para producción en serie, habría que optimizar fuertemente los costos, en particular el de algunas piezas complejas como son las que integran el conjunto de dirección.
Y para cerrar, un comentario totalmente mundano: si una persona pudiese llegar a pensar que circular en un ecoPT podría ser una buena situación para iniciar una conversación casual con una persona del otro sexo, mejor que lo piense dos veces, él o ella tendrían mejores posibilidades utilizando alguna alternativa mas convencional (como ser un Porsche, por ejemplo).
Por Luis Buresti Autor: Luis Buresti